Die Bibliothek des Gewinderollens – 6/9
In diesem Blogartikel erfahren Sie mehr über das Herstellen von gerollten Gewinden, das Rohmaterial, die Phasen des Gewinderollens, die Zeit und Dauer, die richtige Temperatur sowie die Überwachung.
Unabhängig von den einzelnen Verfahren oder Varianten ist es beim Gewinderollen immer eine keilförmige Werkzeuggeometrie, die in den Rohteilwerkstoff eindringt. Dabei verdrängt das Werkzeug das Material, welches bei dem Vorgang in die Freiräume der Werkzeugkontur fließt. Der Vorgang ist beendet, wenn entweder die beabsichtigte Auffließhöhe des Werkstoffs erreicht oder die Werkzeugkontur mit Material ausgefüllt ist.
Rohmaterial
Für das Gewinderollen muss das Rohmaterial rotationssymmetrisch sein, also zylindrisch mit einem konstanten Durchmesser. Aber auch dickwandige Rohre und andere Hohlkörper eignen sich unter Umständen zum Rollen. Filigrane Werkstücke wie z.B. dünnwandige Rohre eignen sich dafür jedoch nicht, denn der Werkstoff fließt bei großer Änderung der Materialstärken in alle Raumrichtungen. Der erforderliche Durchmesser des Rohteils wird auf der Grundlage von Erfahrungswerten festgelegt oder kann rechnerisch ermittelt werden. Entscheidend sind zwei Parameter: das Abwicklungsverhältnis zwischen dem Werkstück und dem Werkzeug sowie das für die beabsichtigte Endform erforderliche Fließvolumen des Werkstoffs.
Materialvoraussetzung: mindestens 6 % Dehnung
Grundsätzlich ist jeder Werkstoff für das Gewinderollen geeignet unter der Voraussetzung, dass er sich überhaupt plastisch verformen lässt. Mit anderen Worten, das Material muss eine Dehnung von über 6 % zulassen, ohne bei dem Vorgang des Gewinderollens zu Bruch zu gehen.
Max. 1200N/mm2 Zugfestigkeit
Bei den Angaben über die maximal zulässige Zugfestigkeit – z.B. kf0 = 1200N/mm2 – stellt sich weniger die Frage nach der Verformbarkeit des Werkstoffs, sondern vielmehr die Frage nach einer vernünftigen Lebensdauer des Werkzeugs. Denn je niedriger die Zugfestigkeit und je korrekter der Durchmesser desto länger ist die Lebensdauer des Werkzeugs.
Zu berücksichtigen ist, dass der zu rollende Werkstoff den Ablauf der Umformung sowie die von der Maschine aufgebrachte Rollkraft und die Standzeit der Werkzeuge massgeblich mitbestimmt.
Ursächlich für die Verformbarkeit von Metallwerkstoffen sind ihr kristalliner Aufbau und ihre chemische Zusammensetzung. So verändert der Kohlenstoffgehalt die Verformbarkeit von Stählen wesentlich: Mit zunehmendem Gehalt nimmt die Möglichkeit der Formgebung ab und die Tendenz zur Kaltverfestigung steigt.
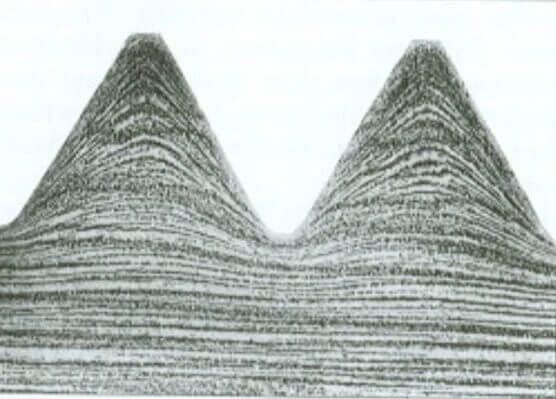
Die Verfestigung des Werkstoffs während der Verformung ist bei der Beantwortung der Frage nach den für das Gewinderollen geeigneten Werkstoffen besonders zu berücksichtigen. Die Verfestigung basiert auf komplexen plastomechanischen Vorgängen in der Kristallstruktur und ist am geschliffenen Querschnitt eines gerollten Gewindes nachweisbar (Abb.1). Man kann nicht genügend darauf hinweisen, dass Werkstoffe, die sich verfestigen, zwar hochbelastbare Bauteile ergeben, der Rollvorgang jedoch besondere Massnahmen und viel Erfahrung erfordert.
Phasen des Gewinderollvorgangs
Es gibt drei Phasen während des Gewinderollvorgangs (siehe Abb.2): die Vorbereitungsphase, in der das Werkzeug die Oberfläche berührt, dann folgt die 1. Eindringphase gefolgt von der 2. Eindringphase, wo jeweils das Werkzeug in das Material eindringt. Diese drei Phasen werden im weiteren Verlauf nun ausführlicher beschrieben.
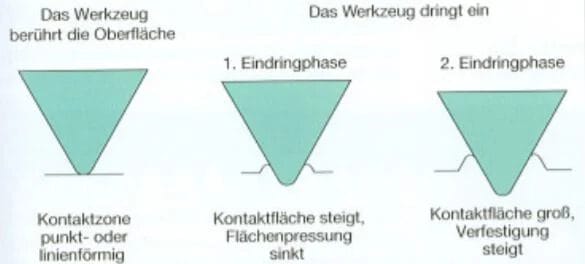
Vorbereitungsphase
Zu Beginn der Umformung berührt das keilförmige Werkzeug die Oberfläche des zylindrischen Werkstücks. Die Kontaktzone ist punkt- oder linienförmig, je nach Geometrie des Rollwerkzeugs. Die Kontaktfläche des Werkstücks mit dem Werkzeug ist zu diesem Zeitpunkt, unter Berücksichtigung der elastischen Eigenschaften der Werkstoffe, klein. Die von der Maschine aufgebrachte Kraft führt damit zu einer Flächenpressung, die in der Regel weit über der Festigkeit des Werkstoffs liegt. In dieser ersten Rollphase, der Vorbereitungsphase, werden derart hohe Druckspannungen in das Rohteil eingebracht, dass sich das Material plastisch zu verformen beginnt.
Erste Eindringphase
In der nächsten Phase des Rollvorgangs, der ersten Eindringphase, drückt sich das keilförmige Werkzeugprofil eher geringfügig in den Werkstoff ein. Das Grundmaterial verändert seine innere Struktur und verfestigt sich nach den beschriebenen Mechanismen des Umformens. In dieser Phase wächst die Kontaktfläche zwischen dem Werkzeug und dem Werkstück und wird deutlich grösser als in der Vorbereitungsphase. Mit dem grösser werdenden Kontaktbereich sinkt jedoch die Flächenpressung, sodass die Maschine eine deutlich größere Rollkraft aufbringen müsste, um die Eindringgeschwindigkeit beizubehalten. Meist arbeitet die Maschine aber bereits in der Vorbereitungsphase mit maximaler Rollkraft. Daher nimmt die Eindringgeschwindigkeit während des Eindringvorgangs in der Regel ab.
Zweite Eindringphase
In der letzten Rollphase, der zweiten Eindringphase, nimmt die Kontaktfläche zu und ist damit deutlich größer als in der ersten Eindringphase. Die einsetzende Werkstoffverfestigung erschwert den Eindringvorgang zusätzlich.
Zeitlicher Verlauf beim Gewinderollen
Der durch die Lücken des Rollwerkzeugs vorgegebene maximale Eindringweg wird je nach Werkstoff unterschiedlich schnell erreicht. Die kontinuierliche Abnahme der Flächenpressung bei gleichbleibender Rollkraft der Maschine und die mit der Umformung einhergehende Werkstoffverfestigung beeinflussen den zeitlichen Verlauf des Eindringvorgangs ganz wesentlich.
Um bewertbare Aussagen zu Rolldauer verschiedener Werkstoffe zu erhalten, müssen alle werkstoffunabhängigen Einflüsse, besonders die Maschinenparameter und die Werkzeuggeometrie, bekannt sein und aufeinander abgestimmt sein. Eine stärke ausgeprägte Profiltiefe und -form erhöhen Rolldauer.
Temperaturverhalten und Kühlung beim Gewinderollen
Die Temperaturerhöhung resultiert aus der äußeren und inneren Reibung während des Rollvorgangs und hängt direkt vom Werkstoff und von den eingestellten Maschinenparametern ab.
Einsatz eines Kühlmediums
In der Praxis wird die Umformung unter Einsatz eines Kühlschmierstoffs durchgeführt, der über das Werkstück und das Werkzeug fließt. Die chemische Zusammensetzung des Kühlmediums und dessen Einsatzparameter sind ein gut gehütetes Geheimnis des Herstellers, denn die daraus entstehenden Qualitätsunterschiede können erheblich sein. Insbesondere bei Durchlaufmaschinen (mehr dazu im Blog 8/9 Durchlaufverfahren) zum Herstellen von Gewindespindeln mit sehr kleinen Steigungstoleranzen sind gleichbleibende Temperaturbedingungen am Werkstück und Werkzeug während des Rollens von entscheidender Bedeutung. Gelingt dies nicht, kommt es zu einem undefinierten Steigungsverzug.
Kühlmittelaufbereitung
Damit die Temperaturbedingungen während des Rollens gleichbleibend sind, werden die Maschinen mit Aufbereitungssystemen ausgestattet, die das zugeführte Kühlmittel in reproduzierbarer Menge, Temperatur und Reinheit zur Verfügung stellen. Die Temperatur des Kühlmittels wird somit im Bereich von ±1,5 °C konstant gehalten.
Die Temperaturveränderung des Werkstücks verrät, wie gut der Fließvorgang getroffen wurde. Tendenziell sollte sich der Grundwerkstoff nicht oder nur wenig erwärmen. Der Experte weiß aus Erfahrung, wann er welches Medium zum Kühlen einsetzen muss.
Überwachung
Die Steuerung und Kontrolle des Rollvorgangs erfolgen auf unterschiedlicher Art und Weise. Zu unterscheiden ist die Produktion auf konventionellen Gewinderollmaschinen, auf denen etwa 90% der gerollten Gewindeteile hergestellt werden, und die CNC-Fertigung (Computerized Numerical Control), auf denen nur unter 10% hergestellt werden. Die heute in der Praxis verwendeten Mess- und Überwachungssysteme erfassen Größen, deren zeitliche Veränderung den Umformvorgang beeinflusst. Die gemessenen Parameter können Kräfte, Drehmomente oder Leistungen sein.
Werkstückvermessung
Um in der konventionellen Fertigung ein optimales Werkstück zu erhalten, ist der Vorbearbeitungsdurchmesser, auf den die Verformung aufsetzt, genau einzuhalten. Dazu werden die Werkstücke an geeigneten Stellen des Produktionsprozesses mehrmals vermessen.
Erfolgt die Bearbeitung des Werkstücks auf einer CNC-Maschine, werden die Eindringtiefe und die Eindringgeschwindigkeit des Werkzeugs in das Werkstück über die jeweilige Benutzeroberfläche vorgegeben und in einem Programm hinterlegt. Die Steuerung überprüft die Werte bei der Bearbeitung stetig und regelt entsprechend nach. Dies ermöglicht eine Kompensation von Homogenitätsdifferenzen im Material, die einen unterschiedlichen Belastungszustand der Maschine verursachen.
Bildverarbeitungssysteme und mechanische Messeinrichtungen
In der industriellen Praxis finden dazu Bildverarbeitungssysteme oder mechanische Masseinrichtungen Anwendung. Diese lassen sich auch zur Bewertung der Werkstücke nach der Bearbeitung einsetzen.
Rollkraft-Erfassungssysteme
Ein Sonderfall sind Anlagen zur Décolletage, mit denen Klein- und Kleinstteile für die Uhrenindustrie in Millionenserien gefertigt werden. Bei diesen speziellen Anlagen wird das zu bearbeitende Material vollautomatisch als Stangenrohlinge zugeführt. Der Umformvorgang im Einstechverfahren wird durch den Einsatz von Rollkraft-Erfassungssystemen geprüft und bewertet. Diese Systeme erfassen den Kraft- oder Drehmomentverlauf über einen definierten Weg oder auch über eine vorgegebene Zeitspanne. Anschließend erfolgt eine Bewertung der beiden aufgezeichneten Parameter. Daraus ergeben sich Hüllkurven, die weder über- noch unterschritten werden dürfen.
Eine weitere Möglichkeit der automatisierten Überwachung ist die Definition von Fenstern, durch die der Kraftverlauf zwingend führen muss. Erfüllen die Werkstücke diese Kriterien nicht, werden sie ausgeschleust. Diese Verfahren geben indirekt Auskunft darüber, ob der Vorbearbeitungsdurchmesser oder das Material den Vorgaben entsprachen. Sie können sogar einen beginnenden Werkzeugbruch signalisieren.
Erfahren Sie im nächsten Artikel, wieso der Rollprozess beendet werden muss, noch bevor die vorgesehene Form erreicht ist und woran der Fachmann dies erkennt.
> Die Bibliothek des Gewinderollen Blog 7/9
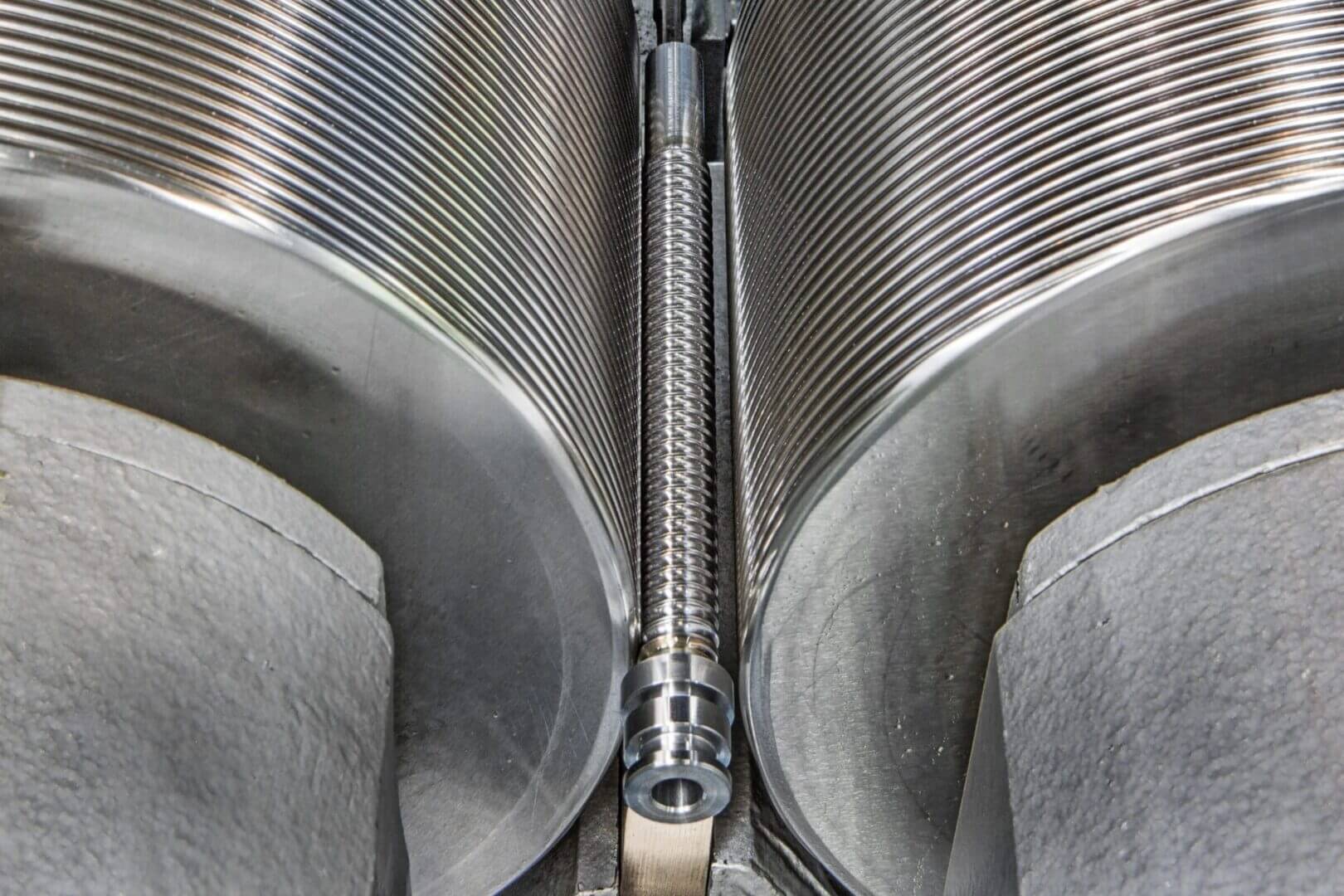
Eichenberger – Ihr Dienstleister von Beginn an
Mit Eichenberger können Sie Ihre individuellen Anforderungen an einen Gewindeantrieb schon mit Beginn der Entwicklung umsetzen. Zögern Sie nicht und kontaktieren Sie uns noch bevor Sie überhaupt wissen, was Sie benötigen. Wir entwickeln gerne mit Ihnen Ihre individuelle Lösung für Ihr Gewindesystem. Nehmen Sie direkt Kontakt zu einem unserer Experten auf, wir sind für Sie von Beginn an da.
> Jetzt unverbindlich kontaktieren und informieren
Mit modernsten Fertigungsmethoden, langjährigem Fachwissen und einem Werkzeugbestand von über 1000 Rollwerkzeugen realisieren wir gerollte Gewindetriebe, die selbst die aussergewöhnlichsten Anforderungen erfüllen:
- Steigungen bis 6 x Durchmesser
- Steigungsgenauigkeitsklasse G5
- Spindellängen bis zu 6 Meter
- Spindeldurchmesser von 2 bis 160 Millimeter
- Sämtliche Normprofile (M, Tr, UNC, UNF, UNEF, Whitworth)
- Mehrgängige Gewinde, auch als Rechts-/Linksgewinde
- Steilgewinde-Profile
- Kugelgewinde-Profile
- Sonderprofile
- Schneckenprofile (besondere Qualitäts- und Preisvorteile!)
- Kerbverzahnungen und Rändelungen
- Konische Gewinde
- Gewinde auf vorgefertigten und/oder unförmigen Teilen, z. B. auch auf Schmiedeteilen
- Freigestaltete Gewindegeometrie
- Eingehen auf Kundenanforderungen, wie z.B. individuell angepasste Mutterngeometrie
Eichenberger überlässt nichts dem Zufall und legt höchsten Wert auf Qualität. Dies überzeugt schon seit 1953 unsere Kunden. Überzeugen auch Sie sich:
> 100% Swiss Quality
> Gewindespezialist seit 1953
Technische Grundlagen Gewinderollen
Literatur und Quellen
Apel, H. (1952). Gewindewalzen: Kaltverformen von Präzisionsgewinden und Spindeln. Hanser.
DeWiki (2022, 3.August). Lexikon Gewinde. https://dewiki.de/Lexikon/Gewinde
Kübler, K. & Mages W.J. (1986). Handbuch der hochfesten Schrauben, (1. Aufl.). Girardet.
Peters, H. (2003). Mathematisch-Technisch-Algorithmisch-Linguistisches Sammelsurium. http://www.hp-gramatke.de
Trösch, B. & Husistein, K. (2007). Bibliothek der Technik -, Band 286, Gewinderollen. Moderne Industrie.
Verein Deutscher Eisenhüttenleute (1984) (Hrsg.). Werkstoffkunde Stahl, Bd. 1. Springer,
Wikipedia (2022, 3. August). Metrisches ISO-Gewinde. https://de.wikipedia.org/wiki/Metrisches_ISO-Gewinde
© 2007 Alle Rechte bei sv corporate media, D-80992 München http://www.sv-corporate-media.de
Abbildungen: Nr. 1, 23-25 RWT Rollwalztechnik GmbH, Engen; Nr. 2 Foto Deutsches Museum, München; Nr. 3 Musée du tour automatique et d’histoire de Moutier, Moutier (Schweiz); Nr. 16 Fette GmbH, Schwarzenbek; Nr. 18 Meinrad Plaz, Staufen (Schweiz); Nr. 26 Habegger SA, Court (Schweiz); Nr. 34-36 FBT Fahrzeug- und Maschinenbau AG, Thörigen (Schweiz); Nr. 37, 38 Schleuniger AG, Thun (Schweiz); Nr. 39, 40 Max-Planck-Institut für Physik (Heisenberg-Institut), München; Nr. 41 Saurer AG, Arbon (Schweiz); Nr. 42 Line Tech AG, Glattbrugg (Schweiz); alle übrigen Eichenberger Gewinde AG, Burg (Schweiz). Satz: abavo GmbH, D-86807 Buchloe. Druck und Bindung: Sellier Druck GmbH, D-85354 Freising. Printed in Germany 889030.