The world of drive technology is constantly changing, growing and being challenged. This also applies to the ball and lead screw drives from Eichenberger Gewinde AG in Burg / CH. Speed, load capacity, precision and maximum service life meet smaller, more compact, more adaptable, more robust, safer and more economical. These quality features in turn interact with resource and energy efficiency. Today, the ideal mechanical component must meet the highest performance requirements and should tend to cost less and less, whether in automation, vehicle or mechanical engineering, electronics, the medical sector, the textile industry, graphics, building services engineering, etc.
Goal: Innovations with a head start
For the thread specialist from Switzerland, customer proximity and goal-oriented dialog with partners are the basic prerequisites for sophisticated individual solutions. A deep understanding of the customer's product is crucial to success. This in turn must be combined with a wealth of experience and a high level of quality awareness so that innovations can be realized with a head start.
With a new and revolutionary coupling system on the market, the thread specialist succeeded in developing one of the key design elements for this pioneering, automated version and bringing it from individual production to series production. This coupling system with a cold-rolled ball screw drive, diameter 12 mm, caused a sensation among experts. The outer contours virtually determined the inner workings of the ball screw drive (KGT). One of the major challenges was to find the perfect solution in an absolutely confined space, while taking into account all other requirements in accordance with the specifications. The entire KGT unit had to be dimensioned downwards. When development, production and quality assurance come from a single source, the flexibility in the manufacturing process or in the creation of prototypes, including thread rolling tools, is remarkably high. This is the case at Eichenberger. Thanks to these factors and the modern machinery, flexible and competitive production is possible even at expensive locations.
The cleanly tuned clutch process demands the utmost in terms of dynamics. With a travel distance of 50 mm, a load of 0 to 2000 N (Newton) is required within 20 ms (milliseconds). The Carry type ball screw can easily withstand these concise requirements between dynamic forces and movement variables, and the cold forming in the non-cutting production process produces a very precise profile geometry, while the thread rolling results in a high surface quality. The extremely low roughness values (≤ Rz 1.0) on the thread flanks have an extremely positive effect on strength, running properties and therefore service life.
What is behind the quality features?
What sounds so simple in the case of the new type of clutch system described at the beginning of this article required a great deal, namely a whole 6 years of basic research and development time in the areas of dynamics and lubrication. Lifetime lubrication is demanding and tricky to guarantee. We are talking about 7-digit, highly dynamic load changes at up to 5800 revolutions. The impressive efficiency of the Carry ball screw drive of over 90 % over the entire service life required extensive testing. Some of the endurance runs extended over 6 months. The lubrication tests alone to achieve the service life took more than 2 years. For the special KGT of this new type of clutch, the team developed a test concept according to customer requirements, taking into account the specifications. Only when the entire unit works together perfectly (spindle, nut, balls, lubrication) can the highest customer requirements be met. Due to the tight tolerances for torque, axial play and concentricity, 100 % checks are carried out on the fully assembled screw drives on a special test bench. The KGT unit with the special "inner world of the nut" is marked by laser. The content of the final inspection can be traced 1:1 via the registered data matrix code.

Quality is the key to success
Quality assurance plays a major role in determining the long-term success of a company. This makes it all the more important not only to maintain quality at a consistent level, but ideally to constantly improve it and adapt it to constantly changing conditions and requirements. To successfully master this challenge, active, continuous development work is required in the value creation process. The high-tech testing systems from Eichenberger are indispensable in many phases of these process chains.
Wear comparison test
In the Research and Development department, endurance tests are carried out to compare different geometries, lubrication and service life. A special test rig for wear comparisons is loaded with weight and tests with a continuous load on one side. The accelerations and decelerations as well as the speed and travel distance can be programmed via parameters. For example, the behavior of the lubricating film on the KGT during fast or oscillating use is displayed, and grease degradation and contamination are observed and evaluated. How do the tribological properties of the different lubricants compare? Does the temperature change due to signs of wear, does the noise change? At what point does profile deformation occur? Investigations beyond total failure continuously build up knowledge. This reveals exemplary combinations of spindle, nut, balls and lubricant that meet the required specifications. This high-performance testing system has become indispensable in the field of research and development. It experiments with several million cycles in one test run without complaint. The resulting knowledge is extremely valuable.
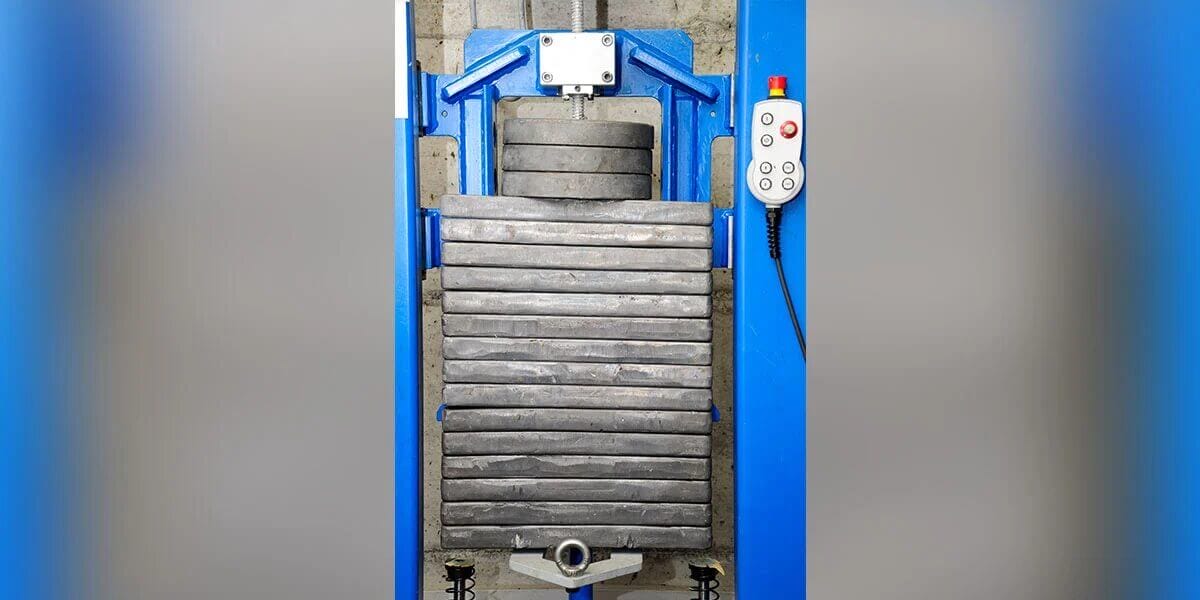
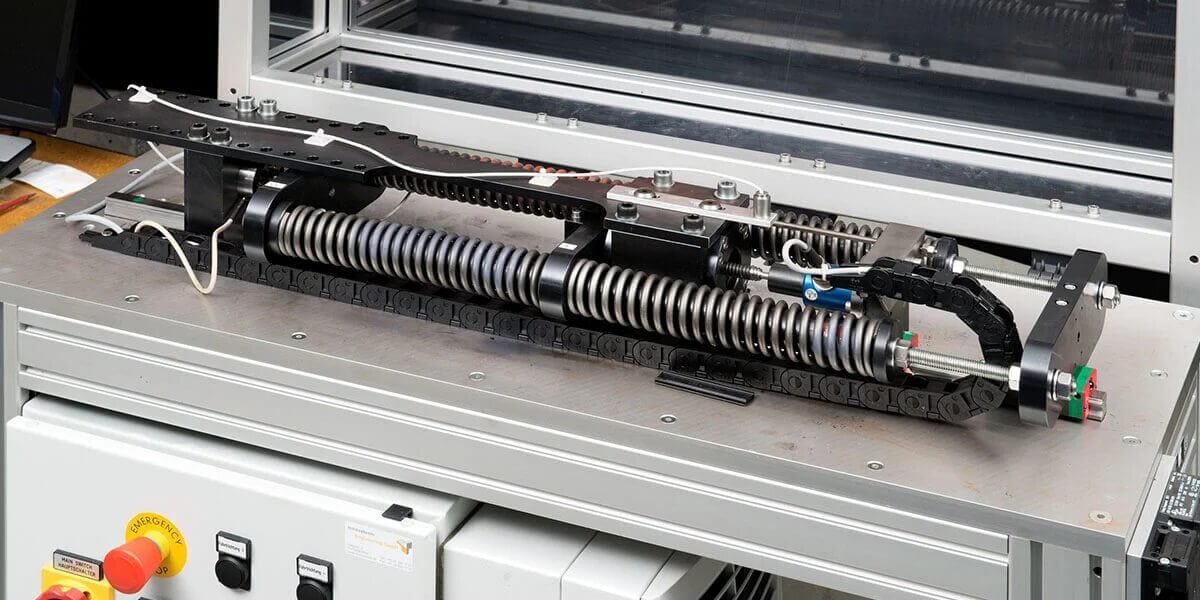
End-of-line testing
Quality is the correspondence between actual and target. The customized end-of-line test systems are used for testing and for the final 100 % inspection of the fully assembled ball or lead screw drives to ensure their functionality. Simplified operating conditions are simulated for the shortest possible periods of time. The torque and axial play of the complete drives are measured. The running behavior is tested within the predefined tolerances. Special software evaluates the measurement signals and compares them with the previously programmed target and actual values of perfect screw drives. The test decision is made on the basis of these measured values. The data reference is applied to the ball screw or lead screw by means of permanent laser marking as a data matrix code. This 2D code allows the origin and stored values of all components to be traced transparently.
Customer-specific tests, trials, measurements
Based on the know-how gained over many decades, Eichenberger is constantly developing modern and highly dynamic testing solutions for the latest developments in its own range or for customer-specific applications. The tests and analyses tailored to the respective projects and screw drives are essential for the research and development work of the design engineers. At the same time, internal quality monitoring of production can be carried out. The complex test benches for customer-specific tests and future developments can be loaded on one or both sides. In principle, they simulate real operating conditions under reproduced conditions. The functions are carried out using freely programmable parameters. Important mechanical test parameters such as force, torque, concentricity and axial play are monitored and recorded. The efficiency is calculated continuously. Any noise is recorded and the lubrication behavior and temperature curve are also measured and noted. These test systems consist of a unique combination of mechanics, sensors, controls and software.
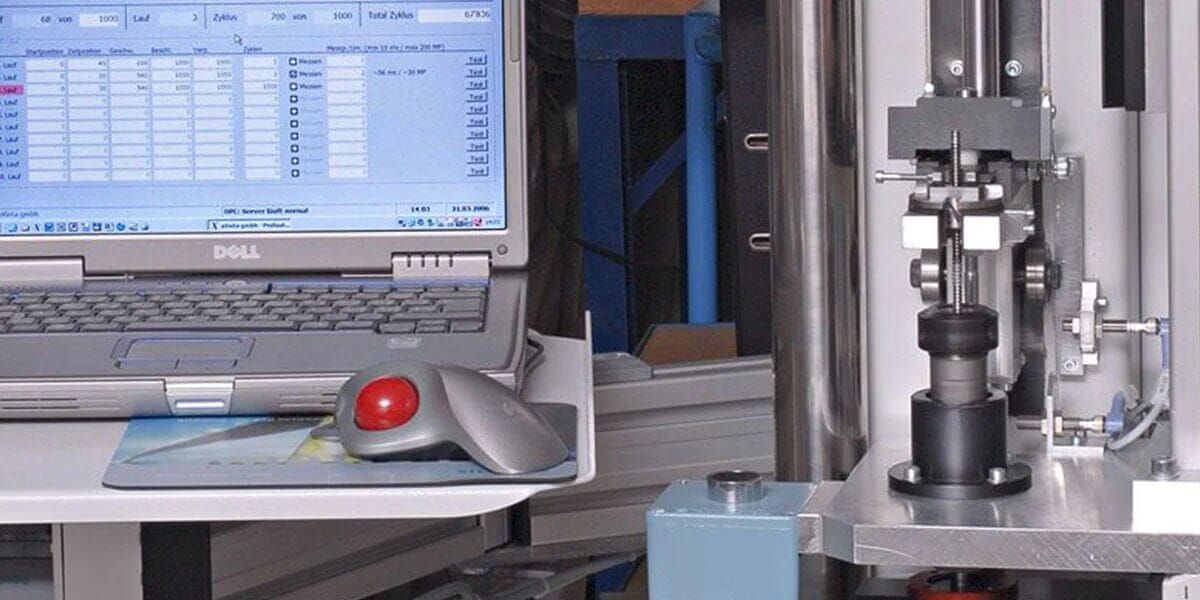
What is thread rolling?
The core manufacturing competence of Eichenberger Gewinde AG lies in thread rolling. The thread profiles of Eichenberger thread spindles are therefore manufactured exclusively using this process. Thread rolling (often also called thread rolling) is the cold forming of the outer surface of round steel parts. A thread is produced by deforming a workpiece under radial-dynamic force between the two rotating rolling tools. As the rolling tool profiles penetrate the surface of the workpiece, the cold material is pressed into the base of the thread rolling tools and thus rolled up to the nominal dimension.