Metallurgical fundamentals
Thread rolling is a prime example of the efficiency and precision of the Cold forming. This process combines material protection, dimensional accuracy and durability - properties that are indispensable in modern technology. In this article, you will learn how the Cold forming and why it is important for the production of rolled threads is so important.
What is cold forming?
The Cold formingalso known as cold forming, is a process in which materials are plastically deformed without prior heating. The small rise in temperature caused by the forming process itself (self-heating) is neglected in this definition of the term. The changes in material properties caused by cold forming are therefore permanently retained. The material remains below its recrystallization temperature, whereby:
- Structural changes minimized become.
- Higher strengths can be achieved by work hardening.
- An exact Dimensional accuracy is achieved.
The generic term cold forming covers several processes. In the context of this technology blog, however, cold forming is only considered in connection with the thread rolling processes described later.
Advantages of cold forming in thread rolling
The Thread rolls is one of the most important applications of cold forming. The threads are formed by plastic flow of the material without any loss of material. The advantages are
- Improved surface quality without reworking.
- Higher load capacity due to uninterrupted fibers in the material.
- Efficient use of resources through minimal waste.
Requirements for cold forming
Any type of cold forming first requires the basic ability of a material to undergo plastic deformation. In principle, plastic deformation in the workpiece is only possible if the external shear stress applied to the material exceeds the critical internal shear stress. However, the fracture strength (breaking strength or shear strength) must not be reached at any point on the part. The deformation can therefore vary locally. If critical conditions are already present at one point, the base material may not show any change at all at another point.
Both solid semi-finished products and flat products (e.g. sheet metal), whose width is much greater than the thickness, can be cold formed. However, the forming result depends largely on the type of semi-finished product. It is always a three-dimensional process.
Designation of cold formability
The behavior of a material during cold forming cannot be described by a single parameter. Several properties of the material as well as the influence of the forming tool and the selected forming process must be taken into account.
Dimensional stability and dimensional stability
The cold formability of a material can basically be characterized by two properties: the ductility and the forming capacity. The deformation resistance is the mechanical stress required for plastic flow - this is why it is also referred to as the yield stress or yield point. The yield stress can be used to estimate the force required for forming and the expected material properties after forming, but not the expected shape.
This upper limit of plastic deformability is referred to as the deformation capacity. As an external sign, the first cracks or even breakage occur. The well-known tensile test serves as an illustration: After exceeding the yield point (transition from elastic to plastic behavior of the material), a reduction in the cross-section (necking) and then fracture occur after a certain elongation. When loading in tension, the elongation at break determined in the tensile test is therefore used as the decisive parameter for the deformation capacity.
The deformation capacity of a material is primarily influenced by the type of stress state, the material temperature and the rate of deformation. This material property must therefore be determined specifically for each cold forming process by means of tests.
Flow curve
The yield curve describes the relationship between the yield stress and the degree of deformation. In somewhat simplified terms, the degree of deformation is the extent of the change in shape. One speaks of an ideal flow curve if the speed of the deformation and the workpiece temperature remain constant during the forming process. In any real forming process, however, the two parameters change continuously. A real flow curve takes into account the respective practical conditions of the forming process, which always depend on the degree of forming. It always differs from the ideal flow curve.
Influences on cold formability
A combination of three material properties is crucial in the practice of cold forming:
- low dimensional stability: Low tension for plastic flow
- good formability: No cracks during forming
- good surface finish: after forming
Influence of the structure
The microstructure of a material plays a central role in the Cold formabilityWithout going into too much depth, it can be said that the material structure has a significant influence on deformation resistance and deformation capacity. If the surface quality depends on the manufacturing process itself, these two properties can therefore be optimized by selecting the appropriate chemical composition of the base material or by setting the most favourable material structure through heat treatment.
Influence of the grid structure
Another material property with an influence on cold formability is mentioned for the sake of completeness, but not explained in detail: Permanent changes in shape during forming are made possible by slip within the individual crystallites. The lattice structure therefore also has a considerable influence on cold formability. This is because the number of preferred slip planes and the slip directions depend on it.
Forming technology
In cold forming, the friction between the tool and the workpiece is a key factor in determining the stress state. Friction, in turn, is decisively influenced by the tool geometry and lubrication. Even though a large number of test methods have been developed to simulate the characteristics of various cold forming processes, these are generally only valid for the underlying workpieces and the selected forming process. The characteristic values obtained can only be transferred to other workpiece dimensions or forming processes with the utmost caution.
Success through experience
It is precisely these variable influencing variables and their effects that mean that experience makes a significant contribution to the success of thread rolling, if not its most important cornerstone. To determine whether the material parameters are within the permissible range, the temperature must be felt and the rolling noise checked, among other things. Special care must be taken to ensure that the process temperature remains low. If this is not achieved, control over the flow process is lost. The result is a bursting of the thread, especially with small core diameters.
Material behavior during cold forming
Self-heating
In principle, the self-heating of a blank has a positive effect on the flow behavior, but the dimensional stability of the thread suffers. As a result of strong self-heating, precision becomes practically uncontrollable.
The rate of deformation has a significant influence on self-heating. However, this is difficult to estimate, let alone quantify. With very slow forming, however, this influence can be neglected.
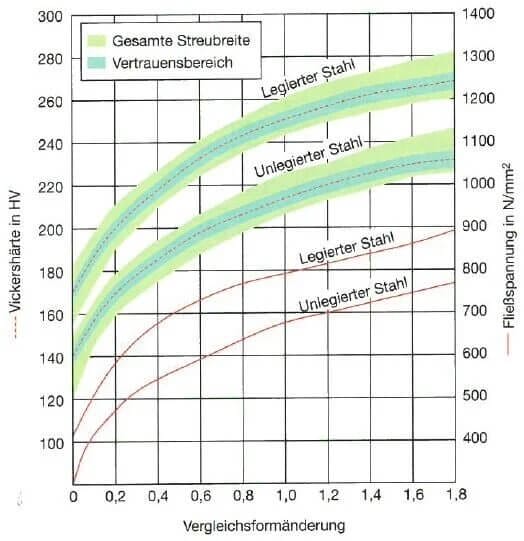
Solidification
In cold forming, the increase in strength values is a desired property in most cases. This hardening - also known as the hardening curve - is proportional to the local change in shape, as shown in Figure 14 for two different steels.
The extent of the hardening also determines the properties of the workpiece produced. The change in shape and the resulting increase in strength can vary greatly locally in a cold-formed workpiece.
Changed properties of the material
As the degree of deformation increases, the yield strength and tensile strength increase, while the uniform elongation (elastic elongation), elongation at break (plastic elongation) and constriction at break decrease, until finally the uniform elongation disappears completely.
Due to the stresses present in the semi-finished product and the stresses introduced by the tool, mechanical stresses of varying magnitude can remain in cold-formed metals after plastic deformation. These tend to lead to tearing of heavily formed areas. An experienced cold former is aware of this.
Limits of the material
Depending on how a material fails, different types of fracture occur. The particularly feared shear stress fractures occur when the greatest (locally occurring) shear stress reaches or exceeds the shear fracture strength. The difference between the shear stress at the start of plastic deformation and the shear or separating fracture strength is therefore important for the formability of a material.
In principle, cold forming is possible with any metal material. In practice, the material must fulfill physical requirements (in particular, it must have sufficient elongation) and it must be possible to comply with the limits of the material. In principle, cold forming is possible with any metal material. In practice, the material must fulfill physical requirements (in particular, it must have sufficient elongation) and it must be possible to observe the limits of the material.
Cold forming of steel
Cold formability Carbon and alloying elements
Steels with a carbon content of more than 1.5% are not suitable for cold forming. Additions of e.g. sulphur, phosphorus or lead generally impair the forming properties. A free-cutting steel containing lead is therefore ideal for machining by turning, milling or drilling, but is only of limited use for cold forming. Alloying or accompanying elements such as manganese, silicon, aluminum and nitrogen have a hardening effect. For this reason, efforts are made to keep their content low during melting and casting.
Steels with a low carbon content and without alloying additions are considered to be very malleable. In such low-carbon and unalloyed steels, the microstructure consists almost exclusively of ferrite grains; the proportion of cementite is low. Up to carbon contents of around 0.35%, the ferrite has a decisive influence on the hardenability of unalloyed and low-alloy steels.
Tool-related shaping limits
If higher degrees of forming are required, intermediate annealing is necessary due to the hardening that occurs. In addition, depending on the material and heat treatment, the tools can withstand a maximum surface pressure of 2800N/mm2 out. As the surface pressure increases with increasing flow stress, the limit of shaping is reached when this value is reached, even if the shaping capacity has not yet been exhausted.
Suitable steels
In addition to unalloyed and low-alloy steels, stainless (chemically resistant) steels are also frequently cold-formed. A distinction is made between ferritic, martensitic and austenitic steels.
Ferritic and martensitic chromium steels
The crystallites of the basic structure of ferritic chromium steels, such as the low-alloy chromium steel type 1.4021, have a body-centered cubic lattice. Such steels have only moderate corrosion resistance. Their hardening behavior is similar to that of unalloyed steels. Martensitic chromium steels, which contain additions of cobalt, molybdenum, nickel or vanadium and also offer only limited corrosion protection, have a tetragonally distorted body-centered microstructure. They are much more difficult to cold form than ferritic chromium steels.
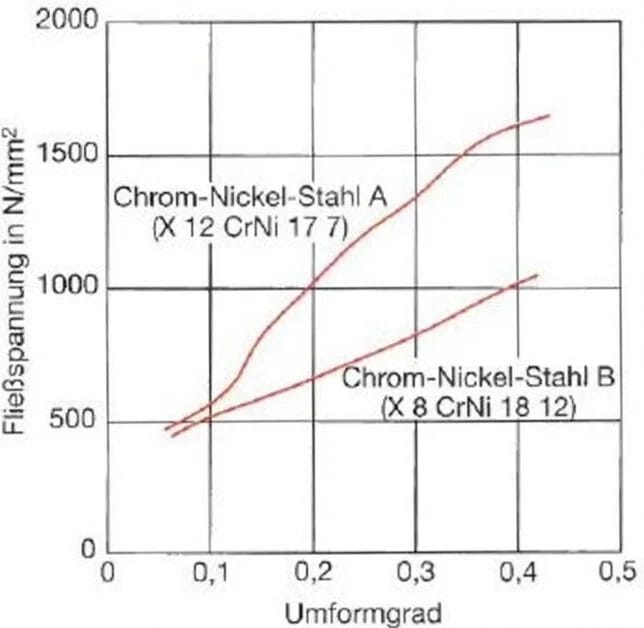
Austenitic steels
In contrast, austenitic steels have a significantly better hardening capacity due to their face-centered cubic lattice structure with its numerous sliding possibilities. As the proportion of alloying elements such as chromium, copper, molybdenum or nickel increases, the hardening of austenitic steels decreases.
Theory and practice
Figure 15 shows the flow curves of an unstable austenitic and a stable austenitic steel determined in the compression test. With approximately the same initial values of yield stress, the yield stress of the unstable austenitic steel, which tends to transform, is around 65% higher than that of the stable austenitic steel after forming. In practice, the results of cold forming generally deviate greatly from those of the compression test.