Threads are indispensable in technology and industry today, but their roots go back more than 4000 years. But what is a thread and how has it changed from its beginnings to modern high-tech manufacturing? The development from early times to modern high-tech manufacturing shows how essential Thread for our technology.
What is a thread?
A thread is a spiral-shaped indentation that runs along the surface of a component. This structure enables the connection of components or the conversion of rotary movements into linear movements. Threads can be found in countless Applications - from simple screws to high-precision machine parts.
The origins of threads - from wedges to screws
It can be assumed that the thread replaced the wedge as a securing element. The realization that a curved surface with grooves provides greater clamping force than a flat wedge must be very old, because the oldest finds of technical threads are more than 4000 years old
Chipless production in the early days
Fibulae found as grave goods were used to hold items of clothing together or to secure pieces of jewelry against loss; such clasps had a short cylindrical core around which a wire was wound in a spiral - in principle, they were therefore chipless fastening threads.
However, there are hardly any surviving fastening threads in the modern sense from Greek and Roman antiquity. The situation is different with moving screws. The Greek mathematician Archimedes of Syracuse (around 287 to 212 BC) is credited with the invention of the screw conveyor. Because the Archimedean screw is simple and robust, it was used to draw water. Today, this moving screw is mostly used to convey sewage sludge or as an extruder in plastic processing machines.
Machined one-off production from antiquity...
Roman doctors used very fine surgical instruments with two screw spindles, i.e. threaded spindles with a matching nut, to spread wound openings. The bronze threaded spindles were first cast as an approximate form and then filed. Due to their smooth running and the evenness of the threads, they can be described as precision mechanical products. The associated nuts - often the yoke of the instrument - were also cast and ground onto the associated threaded spindle. It was not possible to replace the nuts.
Ancient construction cranes and oil and wine presses had screw spindles made of wood, usually oak. The engineers of the time chose large core diameters and thread heights not only because of the forces involved, but also because of the low strength of the wood. This was the only way to prevent the wood from breaking out across the grain. In order to apply threads with a uniform pitch to such large spindles, a triangular sheet metal template was bent around the cylindrical blank and the course of the thread groove was marked. For the next turn, the template had to be shifted by the pitch and applied again. The thread groove, which can be classified between filing and whirling in terms of the process, was worked out by hand - a very simple but sufficiently accurate principle for the time.
...about the Middle Ages...
With the onset of the Middle Ages, technical achievements were lost, as were many of the spiritual conduits of antiquity. Like the spoked wheel, the screw also largely disappeared from everyday life. Only in a few blacksmith's workshops were fastening screws filed from a forged blank and then hardened - but only as individual pieces for a very specific purpose or for personal use.
It was not until the Renaissance that the technology started to move again. The construction of cathedrals, minsters and cathedrals in particular called for lifting devices for heavy loads. Moving screws - albeit still wooden ones - were increasingly used again. The construction of the cathedral in Florence even yielded ball-bearing screw jacks as a further development. As the forces to be transmitted increased and the space for ever larger constructions was not available, the step towards metal movement screws was inevitable.
...until the Renaissance
The first metal screws were intended for military equipment. Screws for the joints of armor were pre-cast as in the days of the ancient Romans and then shaped by filing. The tolerances of these threads did not correspond to today's standards, nor were the screws interchangeable.
It was the scholars of the time who needed ever more precise physical, astronomical and mechanical instruments due to their thirst for knowledge. Optical instruments came from northern Italy, and north of the Alps a precision mechanical craft, watchmaking, was born: seafaring in particular urgently required smaller watches, as accurate positioning at sea was only possible by measuring time.
Return to cold forming
Progressive miniaturization demanded fastening screws whose threads could no longer be produced using conventional methods; even filing was too coarse. Threads were formed in several steps with the help of hardened dies.
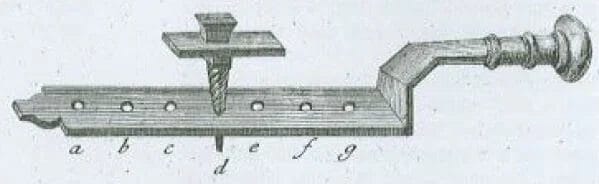
(Source: Schreber, D.G. (ed.): Schauplatz der Künste und Handwerke. Vol.9. Leipzig 1769)
The industrial revolution and standardization
The industrial revolution in the second half of the 18th century led to a surge in demand for mechanical machine parts. New professions emerged and new - sometimes quite exotic - manufacturing processes were proposed. However, none of these processes were able to eliminate the greatest disadvantage of the threads of the time: The screws and the matching nuts were still made individually and by hand.
Preparation of standardization
However, as mechanization in the mines progressed and railroad construction flourished, the industry of the time recognized the urgent need to be able to fall back on interchangeable machine parts. Many tried to find a solution to this problem, but it was Henry Maudslay (1771 - 1831) who succeeded in producing the first threads with a defined diameter and matching constant pitch on his lathe.
The first standard thread
Building on this practical preliminary work, Sir Joseph Whitworth (1803-1887) made theoretical considerations in order to define clear thread dimensions. In 1841, he achieved the breakthrough with the definition of the parameters outer and core diameter, pitch and flank angle. This year is therefore regarded as the year in which the standardized thread was invented. The thread system, still known today as the Whitworth thread in honor of its inventor, was used worldwide at the end of the 19th century, including in mainland Europe. Not even the definition of the metre as the basic unit of length at the 1875 Metre Conference in Paris and the subsequent development of a metric thread system could change this. In the United States of America, thread manufacturers used a mixture of English and metric thread sizes. In principle, little has changed in this coexistence of British, continental European and American thread systems to this day.
Mass production of screws
The standardization of the thread made the screws better, cheaper and finally interchangeable. Strength tables created on the basis of a theoretical analysis replaced the empirical values of earlier engineers when it came to dimensioning. With the advent of machine production at the end of the 19th century, screws finally became a mass-produced commodity.
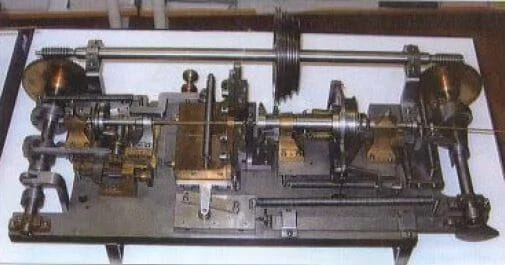
revolutionized thread production in the watch industry
Shortly before the end of the 19th century, the first attempts were made to produce threads by forging. Initially, the process was limited to hot forming. The good flow behavior of the base material was offset by undefined material properties and a poor surface; the strength of the threads also left much to be desired.
Modern high-tech threads - thread rolling
The Thread rolls had already been proposed by the American William Keane around 1835, but was too far ahead of the materials available at the time. The available steel splintered during cold forming. Only when steels with sufficient ductility (elasticity and malleability) became available did success slowly set in: The first results still reflected insufficient knowledge of the relationships between compressive force, deformation and plastic elongation. However, with increasing metallurgical knowledge - much of it from aircraft construction - this process received the necessary impetus; aircraft construction is therefore considered by many to be the "midwife" of massive forming.
Thread rolls in industrial Scale
On an industrial scale, the Thread rolls has only been used since the end of the Second World War. Although it is not known which of the thread rolling processes used today was the first to be used, there is much to suggest that it was the grooving process. With a little imagination, the tools used for this process bear a certain resemblance to the dies of Roman antiquity and the pre-industrial era of the 19th century: The thread pitch is already predetermined by the groove profile of the tool.
Technical principles of thread rolling
Service provider in development
With state-of-the-art production methods, many years of expertise and our tool inventory of over 1000 rolling tools, we produce rolled threads that meet even the most unusual requirements:
- Gradients up to 6 × diameter
- Spindle lengths up to 6 m
- Spindle diameter from 2 to 160 mm
- All standard profiles (M, Tr, UNC, UNF, UNEF, Whitworth)
- Multi-start threads, also as right/left-hand threads
- Steep thread profiles
- Ball screw profiles
- Special profiles
- Screw profiles (special quality and price advantages!)
- Serrations and knurling
- Conical thread
- Threads on prefabricated and/or bulky parts, e.g. also on forged parts
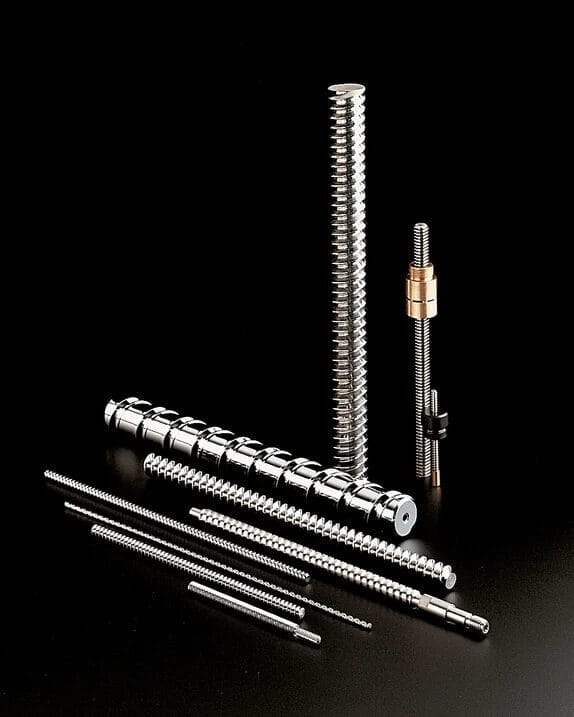
The 9 blogs contain excerpts from the - Library of Technology -, Volume 286, Thread rolls, included.
This book was compiled with the technical support of Kurt Husistein and published by Verlag Moderne Industrie, ISBN 978-3-937889-30-6.
Literature and sources
Kübler, Karl-Heinz, Mages Walter J. Handbook of high-strength screws, 1st ed. Essen: W. Girardet Buchverlag, 1986.
http://www.hp-gramatke.de: Hans-Peters Mathematical-Technical-AlgorithmicA linguistic smorgasbord.Verein Deutscher Eisenhüttenleute (ed.): Werkstoffkunde Stahl, vol. 1 Berlin: Springer, 1984. Apel, Heinz: Gewindewalzen: Kaltverformen von Präzisionsgewinden und Spindeln, Munich: Hanser 1952.
© 2007 All rights reserved by sv corporate media, D-80992 Munich
Illustrations: No. 1, 23-25 RWT Rollwalztechnik GmbH, Engen; No. 2 Photo Deutsches Museum, Munich; No. 3 Musée du tour automatique et d'histoire de Moutier, Moutier (Switzerland); No. 16 Fette GmbH, Schwarzenbek; No. 18 Meinrad Plaz, Staufen (Switzerland); No. 26 Habegger SA, Court (Switzerland); No. 34-36 FBT Fahrzeug- und Maschinenbau AG, Thörigen (Switzerland); No. 37, 38 Schleuniger AG, Thun (Switzerland); No. 39, 40 Max Planck Institute for Physics (Heisenberg Institute), Munich; No. 41 Saurer AG, Arbon (Switzerland); No. 42 Line Tech AG, Glattbrugg (Switzerland); all others Eichenberger Gewinde AG, Burg (Switzerland). Typesetting: abavo GmbH, D-86807 Buchloe. Printing and binding: Sellier Druck GmbH, D-85354 Freising. Printed in Germany 889030.