Digitalization is changing our world. The manufacturing industry is increasingly being shaped by the internet and modern technologies. In the age of automation and miniaturization, mechanical drive elements must constantly meet new and more ambitious requirements in the respective fields of application. The trend in the search for energy-efficient means and solutions continues unabated. This means that development in the field of mechanics is never finished. The Swiss-based company Eichenberger Gewinde AG has recognized these opportunities and is taking advantage of them. It turns out that the smaller and more precise the component, the greater its area of application.
In drive technology in general and medical and optical applications in particular, ever more exceptional dimensional and quality requirements are being demanded. Higher demands require more expertise. After almost seven decades of development work, a spindle solution is available for almost every application - or is being developed - because Eichenberger explores new limits every day in the optimization of machines and tools. Customer-specific tasks are the challenges sought by the thread specialist.
Phenomena from nature
Researchers are constantly working on transferring phenomena from nature to technology. Many new developments are inspired by the animal kingdom and are based on the systematic recognition of solutions from the natural world. Tiny, highly efficient, precise, robust, economical - these characteristics not only apply to the tireless and adapted ant, but also to Eichenberger's miniature lead screw drives. The wood ant can carry 40 times its own body weight, and it is often claimed that a load 100 times its own weight is easy for these "giants of the forest". The situation is similarly extreme with the customized small spindle solutions from the Swiss production company. The smallest, cold-rolled screw drives, for example, with a diameter of just 3 mm, can be loaded up to 2000 times their body weight.
Miniature spindle - to the limits of what is possible - like ants
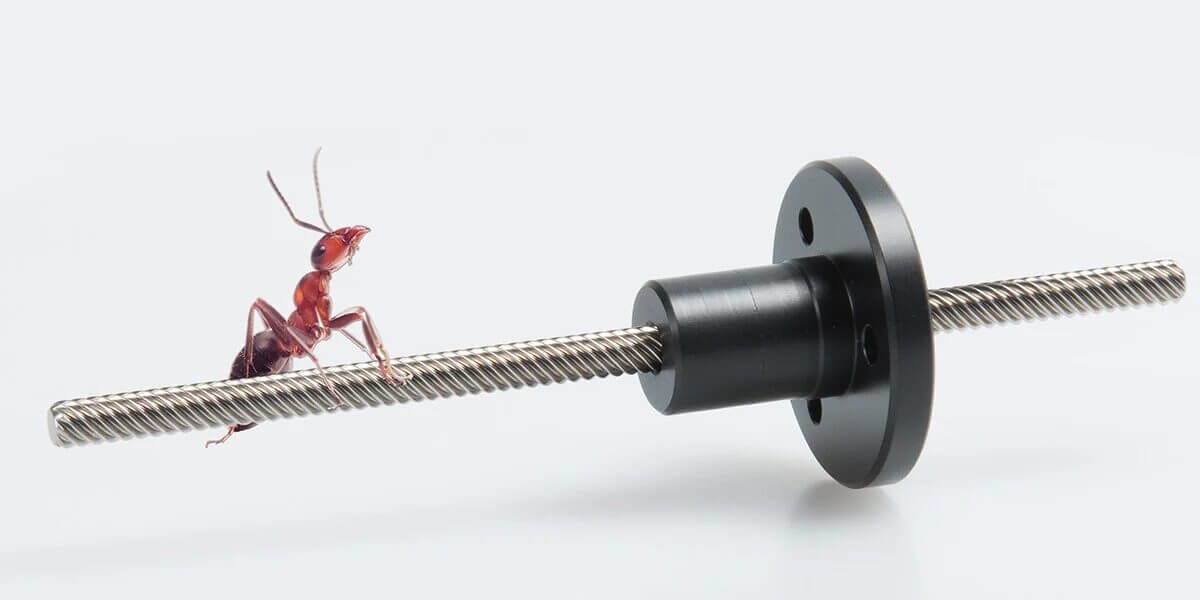
The cold forming of the spindle leads to a considerable increase in the strength of the material; depending on the material, 30 to 50 % are possible. Thread rolling has an extremely positive effect on the roughness values of the thread flanks and in the base radius (around Rz 1.0), the notch sensitivity is very low. The longitudinal fiber of the base material is only deformed, so there is no interrupted fiber flow as with threads produced by machining. The result is a "smoothly rolled", compressed surface, which is essential for a long service life of the spindle. All this leads to a higher degree of efficiency than is the case with cut or ground threads. Coatings can also be applied to further reduce sliding friction and increase service life in collaboration with the perfect coating partner.
What sounds so simple is only possible with extensive know-how in development and manufacturing processes and modern machinery. At Eichenberger, research, development, production and quality assurance work hand in hand. The developers listen to the customer and understand their concerns. Answers are worked out in a consultative, solution-oriented dialog. In addition to miniature dimensions, precision and cleanroom suitability are the driving requirements. Robustness, reliability and value for money are further requirements placed on the design elements. The machining of a filigree profile ø 3 mm x length 300 mm is demanding. The smaller the component, the less leeway there is for deviations. Among other things, the art lies in achieving concentricity and straightness within the tightest tolerances. Thanks to close internal teamwork, flexibility in terms of prototype production is possible within the shortest possible time. The rolling tools are manufactured "in-house". Many years of experience, flexibility and a high level of quality awareness are essential for the high-quality production of such fine, customized threads. As early as the sampling stage, the company focuses on series production.
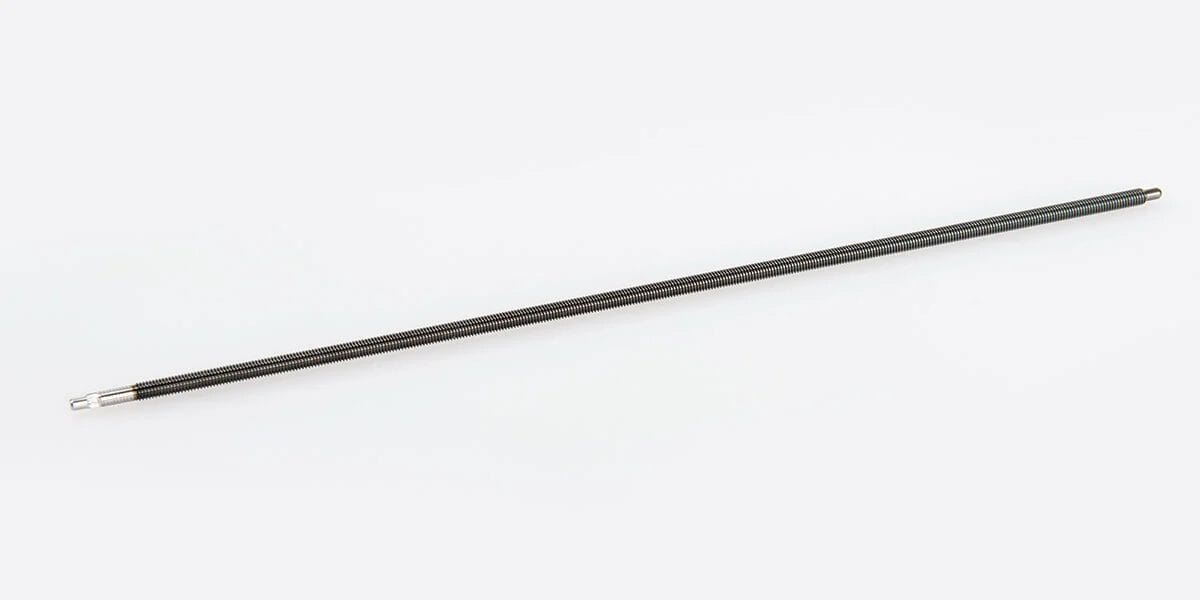
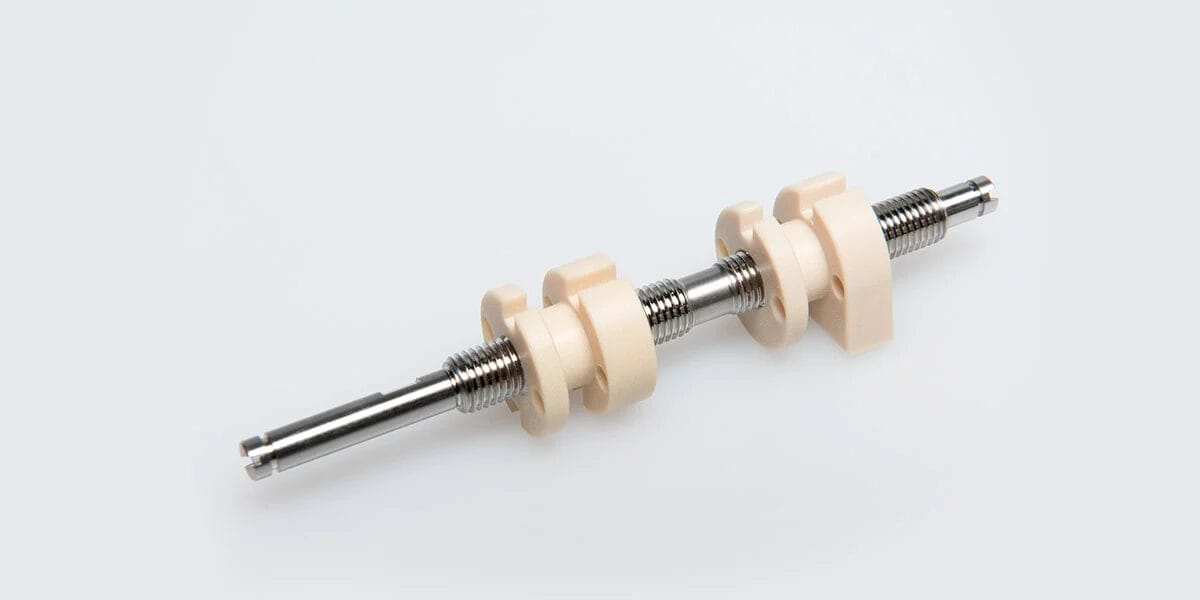
enable a gripping movement. M6 x 0.75 mm
A rolled threaded spindle and a ground threaded spindle are worlds apart in many respects. The price plays a decisive role. Such high lead angles can be achieved with rolled spindles that you can only dream of with a ground design.
Miniature lead screw, optimum screw and nut pairing
Perfectly matching the material of the thread profile and the nut in terms of tribological properties is crucial and can save energy and costs. Raw material resources considerably. The perfect material pairing between the steel spindle - stainless steel or aluminum is also available on request - and the wide variety of state-of-the-art high-performance plastics or bronze for the nut bodies proves to be indispensable. The ideal interaction between the two components means that customer-specific basic requirements such as high temperatures (over 200° Celsius), food conformity, freedom from maintenance and many more can be guaranteed. Outstanding sliding properties with a coefficient of friction of less than 0.1 ensure minimal abrasion and silent running.
The prerequisite for success is dialog with the customer, which is the driving force for innovation. The new or further development of the screw drive as a unit (spindle and nut) guarantees optimum function. The rolled lead screws are characterized by high dimensional accuracy and efficient, fast production is possible, which has a positive effect on the price, especially for large quantities.
"Swiss made" in the international market
Eichenberger Gewinde AG is a company with a defined goal: the rolling (cold forming) of threads and the manufacture of screw drives (spindle/nut).