A dental prosthesis from the very first treatment - this is made possible by a 5-axis scanner with a robotic arm, which sends the oral data obtained directly to a milling machine. It can be used to scan impressions as well as partial and full jaw models in less than a minute. Our miniaturized, cold-rolled ball screw type Carry gives the scanner the best possible positioning flexibility. With this small ball screw, we have developed the key design element for this high-tech application and brought it from individual production to series production.
Digitalization in dentistry is "on everyone's lips"
In today's society, beautiful teeth mean: health, social acceptance and professional success. Advanced techniques can improve and simplify everyday practice work. Digitalization is also advancing at an increasingly rapid pace in dentistry and dental technology. Until a few years ago, dental technology was a branch of craftsmanship that stubbornly resisted digitalization and automation. The production of individual, custom-made parts is not so easy to rationalize. In the meantime, however, the general development of digitalization has also become widespread in these processes due to the numerous advantages for the benefit of patients. Almost every type of dental work can now be designed on the computer and produced by machine.
The fields of automation, miniaturization and digitalization are therefore constantly placing new and extraordinary dimensional and quality demands on mechanical drive elements. Today, even simple design components must be able to meet the highest requirements. With the miniature version of the Carry cold-rolled ball screw, diameter 4 mm, pitch 1 mm, a small component has successfully proven itself. The application-optimized screw drive was available in a short time-to-market, is safe and reliable and guarantees maximum precision and cost-effectiveness.
Classic dental technology
Dental technology is a craft whose task is to manufacture all types of dental prostheses, such as dental crowns, bridges, dentures, etc. Dental work is produced in a dental laboratory. Impressions of the jaws and teeth form the basis for almost all dental work. The dentist mills the tooth to be restored back into a stump. The dental technician produces a plaster model of the teeth from the rubbery plastic impression, which is unpopular with many patients. He then models a wax model on this true-to-size tooth stump, which corresponds to the later crown, for example. Using various casting processes, the shapes of the wax models can be copied 1:1 and dental prostheses can be produced. The experience of many patients shows that this conventional technique is extremely time-consuming and crowns and inlays do not always fit perfectly. Constructions made under stress or dental prostheses made with less skill often lead to unsatisfactory results.
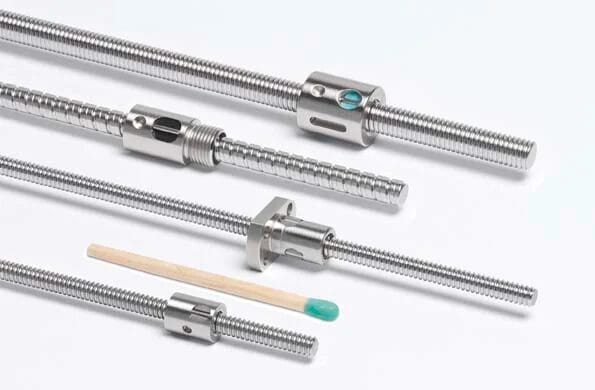
in an impressive dimensional comparison with a match
Ball screws ensure a relaxed visit to the dentist
Dentures without a plaster cast
The computer-aided manufacture of dental prostheses, known as CAD/CAM technology, not only makes life easier for patients, but has also amazed many a dentist and technician. This technology makes it possible to take digital impressions of teeth. It saves time and simplifies the imaging process. The dentist guides the camera head over the teeth while a detailed 3D image in natural colors is created on the screen. The calculated ceramic prosthesis on the screen can be rotated so that, among other things, the contact points to the neighboring teeth, which are also digitally recorded, can be precisely determined. The high precision of this digital data enables the dentist to design a precisely fitting, high-quality ceramic prosthesis. A revolutionary 5-axis scanner with robotic arm and innovative model positioning goes one step further. Thanks to its unique operating concept, scanning in fully automatic mode is also possible manually in record time. It can be used to scan impressions, partial and full jaw models in less than a minute. The 5-axis machine is also able to scan the roof of the mouth, enabling the digital construction of model castings. The Carry 4×1 ball screw, slightly adapted, meets all the requirements to help this new positioning scanner achieve ground-breaking efficiency and flexibility of movement. Special software calculates what the healthy tooth once looked like at this point. It then sends the digital data record to a milling machine, which is usually located in an adjoining room. A high-quality, metal-free and precise dental prosthesis is created in just one session.
Challenge accepted
As a thread specialist, unusual thread forms are the challenges we are looking for. Small, precise and cleanroom-compatible are the driving requirements, particularly in the medical sector. The Carry cold-rolled miniature ballscrew meets these requirements and is now very successful in this market niche. It is the alternative to the high-priced ground screws that were previously used when a miniature dimension was required. Eichenberger's design engineers listen to the customer and understand their concerns. Answers are sought and found in a consultative, solution-oriented dialog. When development, production and quality assurance come from a single source, flexibility in terms of prototype creation, including thread rolling tools, as is the case at Eichenberger, is possible within a very short time. Now it was time to make the step from small series to large series production. The highest quality standards and massive price pressure were the driving force that prompted the developers to reach their goal "via a detour". What sounds so easy only works with a great deal of know-how, a high level of quality awareness among the individual employees and a correspondingly modern machine park. Today, only one machine produces the nut of the ball screw drive. Several operations are carried out on the nut in a single clamping operation. A larger body volume as the starting material, with a special grip option for machining the nut body, coupled with a newly equipped, fully automated and robot-supported production machine was "the move" for the competitive manufacture of the carry nut.
Thanks to our own induction hardening system, the extremely demanding hardening of spindle surfaces is possible (700 - 800 HV5). The threads with a diameter of 4 mm have a core diameter of 3.2 mm. The hardening range must extend from the outer diameter of the spindle to 0.5 mm below the core diameter. To ensure that the threaded rods can withstand maximum loads, it is essential to maintain a soft core. Great expertise is required here.

Diameter 4 mm, pitch 1 mm
Service provider in development
Eichenberger Gewinde AG is a company with clear objectives: The rolling - i.e. cold forming - of threads and the production of screw drives (spindle and nut). Using state-of-the-art production methods and by developing new dimensions, Eichenberger supports the customer in "his" innovation.