Steep lead screws are used wherever a rotary movement has to be converted into a fast longitudinal movement: for example in rotary drives, in swivel motors of dosing and analysis devices or in door closing systems. The original of such a steep lead screw originated in the late 1980s - here in Burg, Switzerland. It was created a quarter of a century ago, the Speedy rolled lead screw, with a diameter of 10 mm and a pitch of 50 mm.
Forward with healthy innovation
When it comes to drive systems, users today are increasingly looking for economical, energy-saving overall solutions with low operating costs. In addition, machine manufacturers expect a technological edge that strengthens their competitive position. This is why the requirements for automated motion sequences continue to grow unabated. This need to solve practical tasks is stimulating and challenging mechanics.
Eichenberger Gewinde AG has dedicated itself primarily to threading technology and has been rolling customized, highly precise and sophisticated motion spindles for almost seven decades. Over the years, the thread specialist has developed its own processes. With a wealth of experience and technical expertise, it supports its partners on the path to innovation.
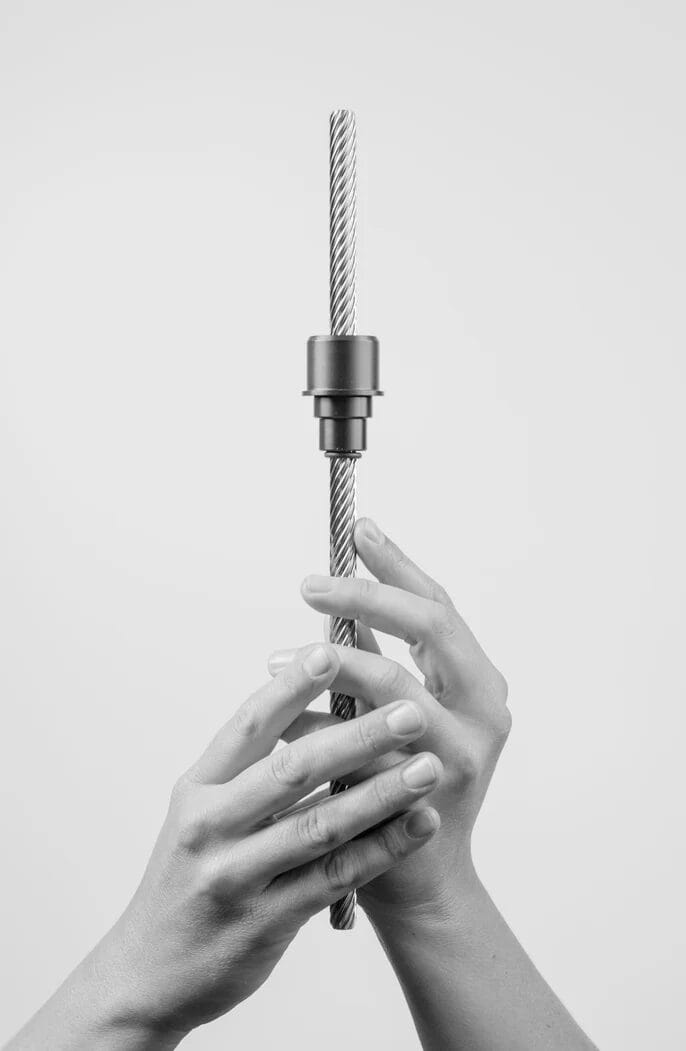
Original type Speedy diameter 10 mm, pitch 50 mm
The journey of the original Speedy began at the end of the 80s
The success story of Europe's "first cold-formed steep thread sliding drive with the enormous pitch ratio of 10 x 50 mm began at the end of the 1980s. A Swiss industrial company was looking for a very precise and reliable drive solution for a new type of measuring system. The servo-hydraulic linear amplifier formed the centerpiece of this ultra-modern testing system. The integrated automation functions, i.e. the positioning or feed tasks, were to be managed by a milled, precision thread slide drive. However, production was extremely expensive. For this reason, the customer was looking for a highly accurate and reliable lead screw that could be manufactured using the cost-effective thread rolling process. In thread rolling, unlike milling or turning, the longitudinal fibers of the material are not cut but deflected. The result is a compressed, smoothly rolled, extremely resilient surface. The company knocked on our door - and it turned out that its dimensional requirements were top-class: A diameter of 10 mm with a 5-fold pitch. Cold-formed sliding spindles themselves had been known for many years, but such high rolled pitches were considered revolutionary at the time.
At the time, tool procurement was very limited and there were no CNC-controlled machines that could meet these requirements. This meant that two challenges had to be overcome at the same time. Firstly, to produce the thread rolling tool for the steep spindle and secondly, to design the right tool for the nut.
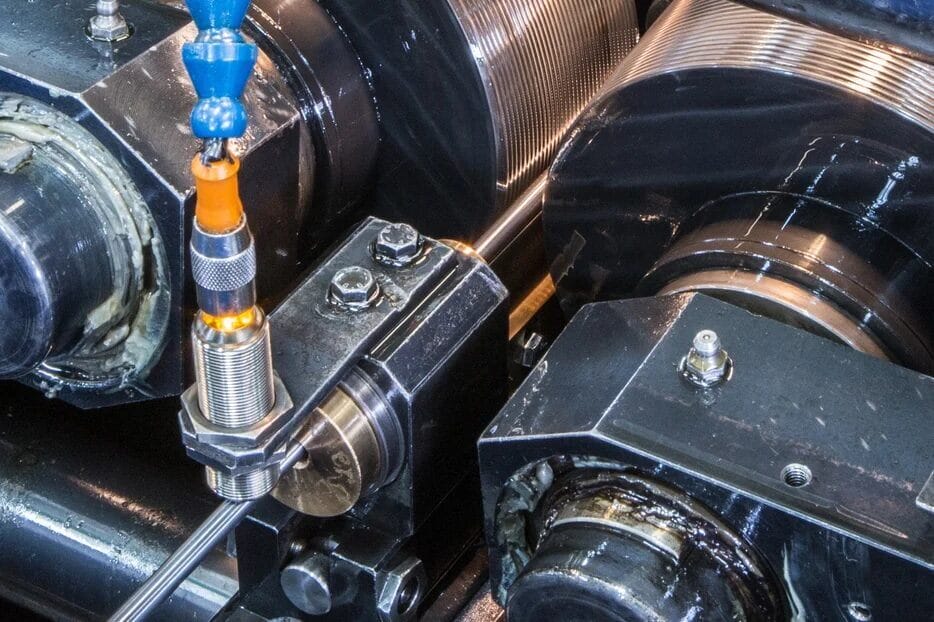
"Who invented it"?
Over the years, our developers at Eichenberger have worked intensively on cold forming technology. This has resulted in a huge amount of know-how and various spindle types in a wide range of dimensions, pitches and, above all, thread profile shapes. Symmetrical and asymmetrical thread forms were developed. Again and again, the designers tinkered with the thread flank angles. Since then, countless customer solutions between 8 and 120° flank angles have been rolled. The shape of the spindle core section has always taken center stage. As a result, basic thread profiles with a roof shape, different radii on the thread core diameter, radius fusions etc. are easy for our production in Burg.
With an extremely efficient efficiency, speed and precision characterize the 10 x 50 mm lead screw. It was rightly christened Speedy. Speedy's exceptional properties are due in part to the perfect combination of the rolled spindle and the plastic nut. There are more than a handful of excellent plastic suppliers who offer technical plastic specialties. The Swiss thread roller maintains contact with them and is independent, as it is not tied to any particular raw material. Accordingly, the right plastic can be selected from the range for the required application and recommended to the customer.
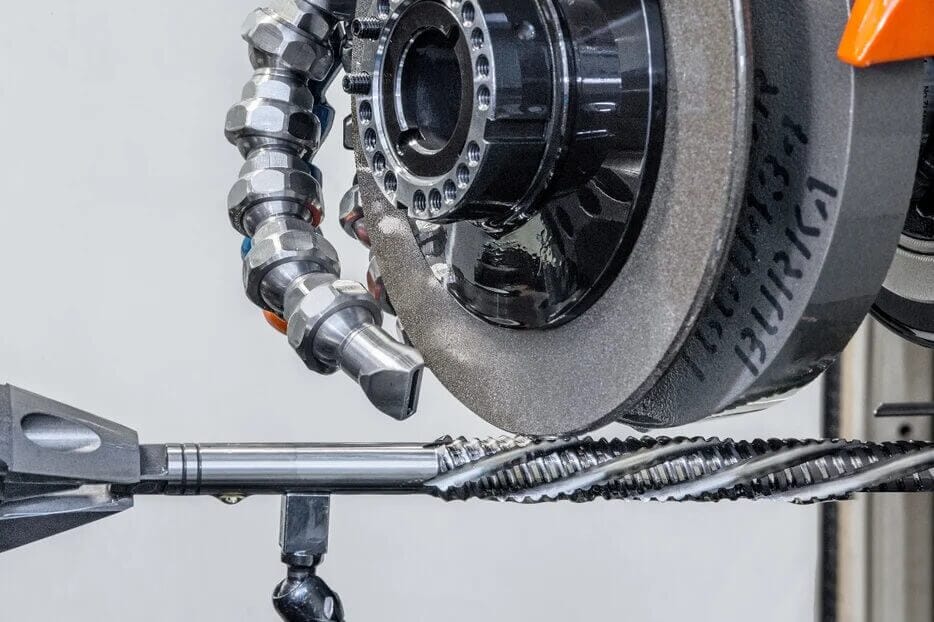
Ultra-thin, minimal initial lubrication
results in 15 times the service life
Speedy is characterized by high abrasion resistance, a low coefficient of friction and absolute freedom from maintenance. Grease-free running is possible in accordance with customer requirements. Unconditional dry running is often required from the outset. During the development process of customized spindle solutions, however, it always becomes apparent that it is precisely in this area that the service life can be massively increased. With careful, minimal initial lubrication, without relubrication, 15 times longer service life values were achieved compared to dry running.
And today: brilliant ideas are continuously being implemented
Eichenberger is your partner for the development and production of your screw drives to measure, in any shape and design. Thanks to our in-house production, we are extremely flexible and can realize even complex products with a short time-to-market. Our passion for perfect motion leads to surprising screw drive solutions that make your products innovative and bring them to the forefront of the market. Extraordinary customer solutions are now developed on request - the most extreme size to date: lead screw diameter 8 mm, pitch 600 mm.