The most important thing in a conversation is to hear what has not been said
(Peter F. Drucker)
At Eichenberger, the customer always takes center stage: Actively listen and ask questions, advise, design, test, optimize, produce. Only through the targeted exchange of information and ideas can needs be fully understood and implemented. In this way, Eichenberger Gewinde AG adapts its products and its value chain to the constantly increasing international change, trusting in its own strength. The thread specialist lives "Acting with foresight instead of reacting" as a vital part of its corporate culture. Its customized ball screws are used everywhere, from medical, electrical and automotive engineering to automation and even aerospace. One very interesting product is the customized ball screw solution for aircraft seat adjusters.
Taking off together
Aircraft seats should be inviting, comfortable and extremely user-friendly. In order to fly more economically and therefore also more ecologically, the focus is not only on the design, comfort and functionality of the seat rows, but also on weight, space saving, durability and quality. The backrest, seat and footrest adjustments of the aircraft seats were previously controlled by three separate mechanisms. With the new adjustment system, all adjustment options can now be regulated at one and the same point thanks to three small, high-precision and robust Carry ball screw drives.
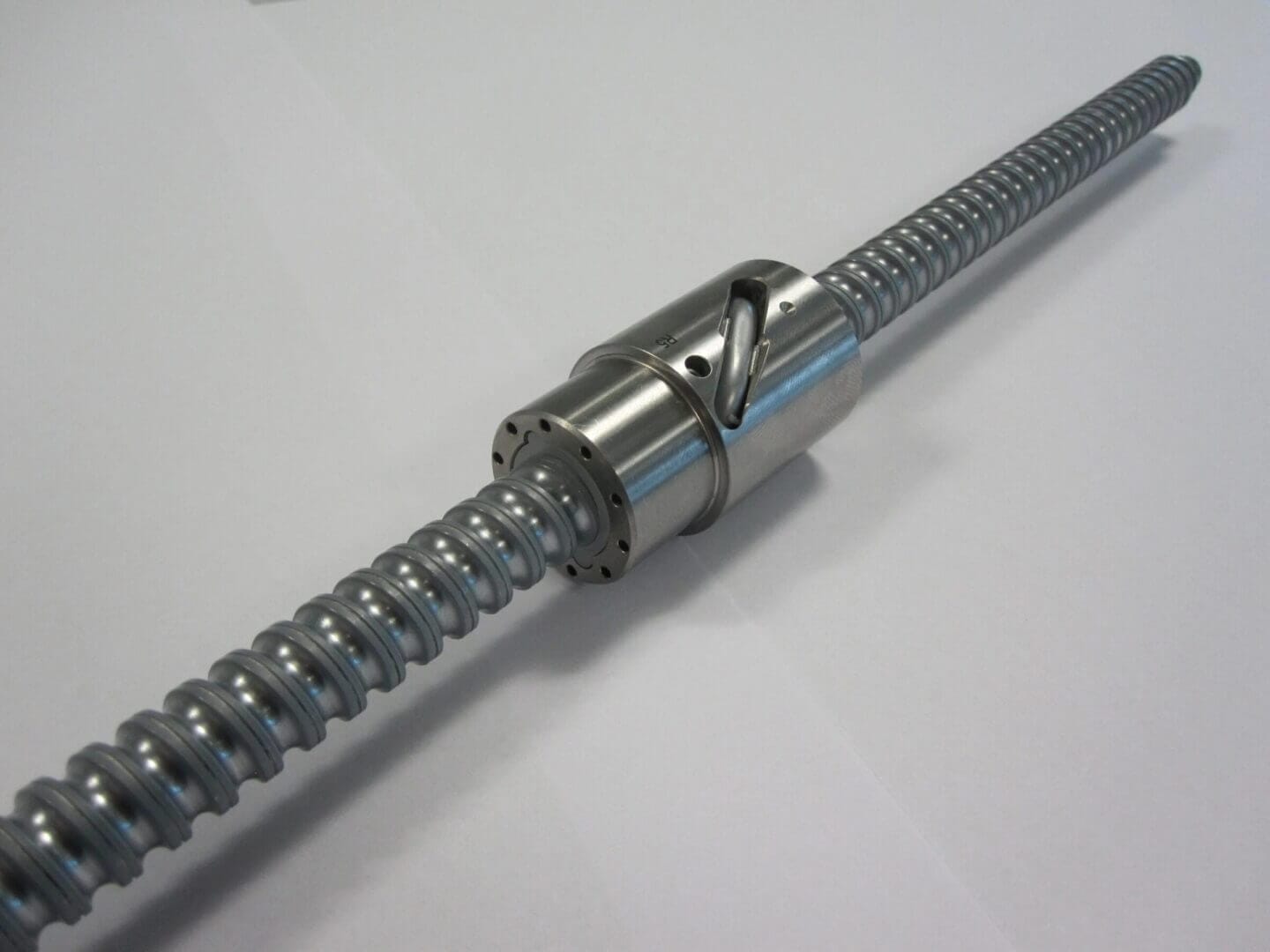
Challenge accepted
In order to save kerosene costs, airlines are increasingly looking for lightweight solutions in aircraft interiors. Furthermore, wider chairs are now being offered for the benefit of passengers. Technological progress is increasing the complexity of systems, and noiseless movements in the smallest of spaces are required. This has a direct impact on the requirements for the geometric environment, dimensions and the dynamic and static load ratings of the drive components.
Based on the specifications, three high-precision, robust ball screw drives had to be determined. The exterior of the nuts had to be adapted to the special specifications. The 10 high-precision holes (ø 1.52 mm) on the face of the ball screw nuts, which are essential for the power transmission of the motor, posed a particular challenge. Metal "lives". Just how "alive" steel can be is clearly demonstrated during hardening. During the hardening process, the metal changes differently depending on the batch and loses dimensional accuracy. These changes cannot be calculated and are unpredictable. Special dexterity was essential when it came to the accuracy of the 10 drill holes in the nut bodies. Measuring, hardening, measuring, hardening - the developers succeeded in adapting the drill holes accordingly, and after vacuum hardening the required high-precision drilling dimensions were achieved, tolerance ± 0.015 mm.
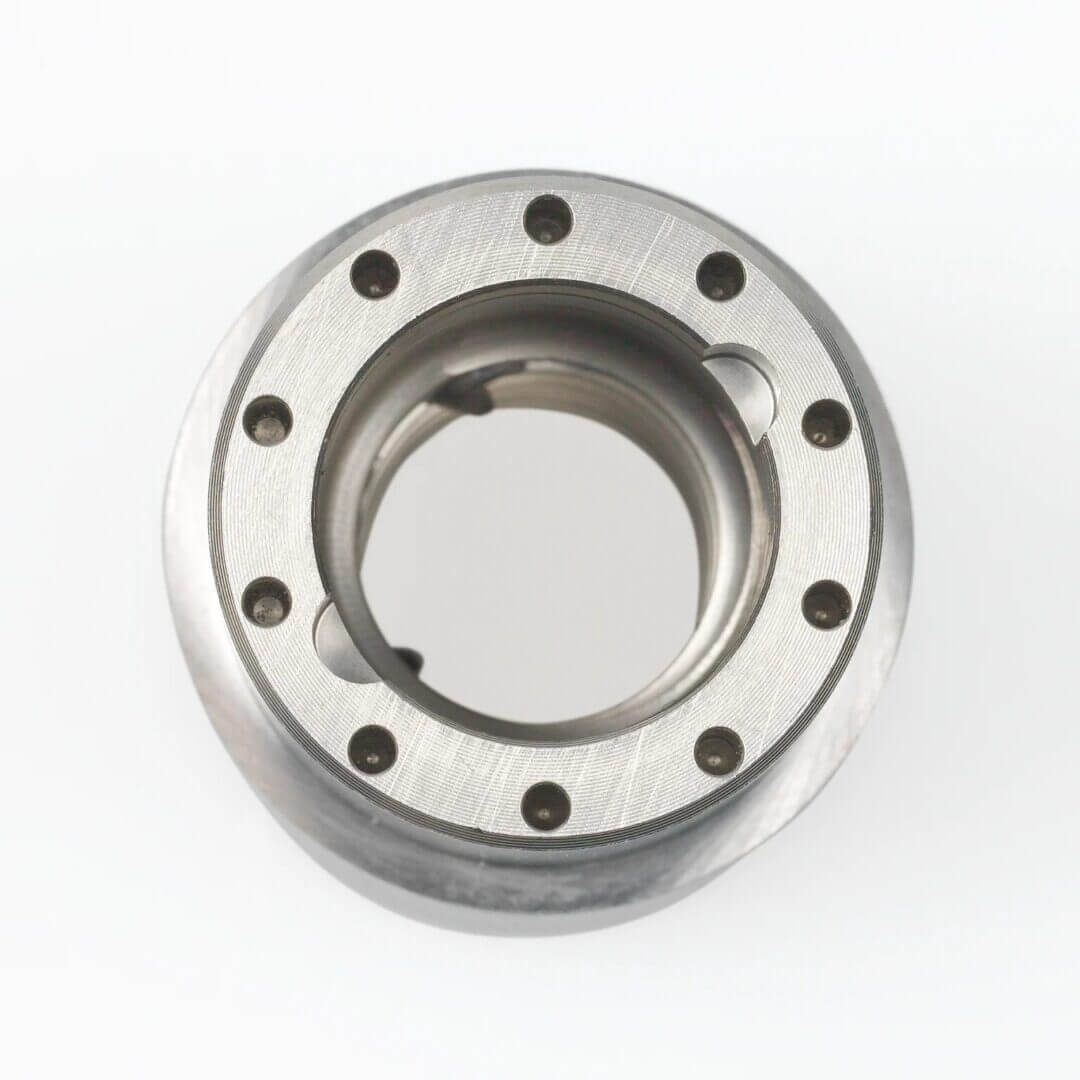
When it came to the accuracy of the drill holes, a special instinct was indispensable
The nuts are hardened to 59-63 HRC. The close and good cooperation with the nut hardening shop enables flexible and time-saving prototype production. Thanks to the automated, sophisticated production process, customer requirements can be met at very short notice. Service life calculations are carried out immediately and the production process can be directly intervened in and reacted to. The supposedly expensive production location of Switzerland initially caused some skepticism among customers. However, the professional advice, fast prototype realization and the interesting price-performance ratio were convincing.
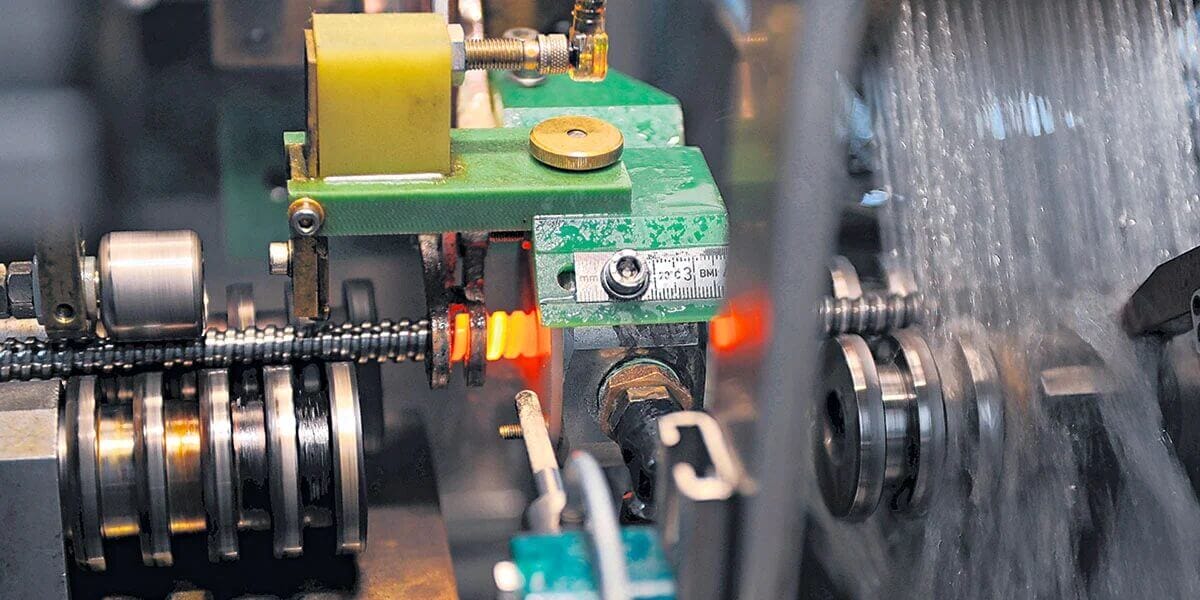
Ideal conditions due to cold forming
What makes the Carry ball screw drive so resilient and the ideal functional element for this application? Thread rolling produces very precise geometries with a high surface quality. The usual manufacturing processes for threads such as milling, turning or whirling are machining processes. These have the disadvantage that they interrupt the grain flow of the steel. On the other hand, thread rolling is a non-cutting process that does not cut the longitudinal fibers, but merely diverts them. Depending on the material, this results in an increase in strength of 30 to 50 %. At the same time, the surface in the profile hardens. This "smooth surface" offers little opportunity for dirt to accumulate. This is crucial for a long service life. Thread rolling also results in very good roughness values (~ Rz 1.0) on the thread flanks and in the base radius, resulting in significantly reduced notch sensitivity.
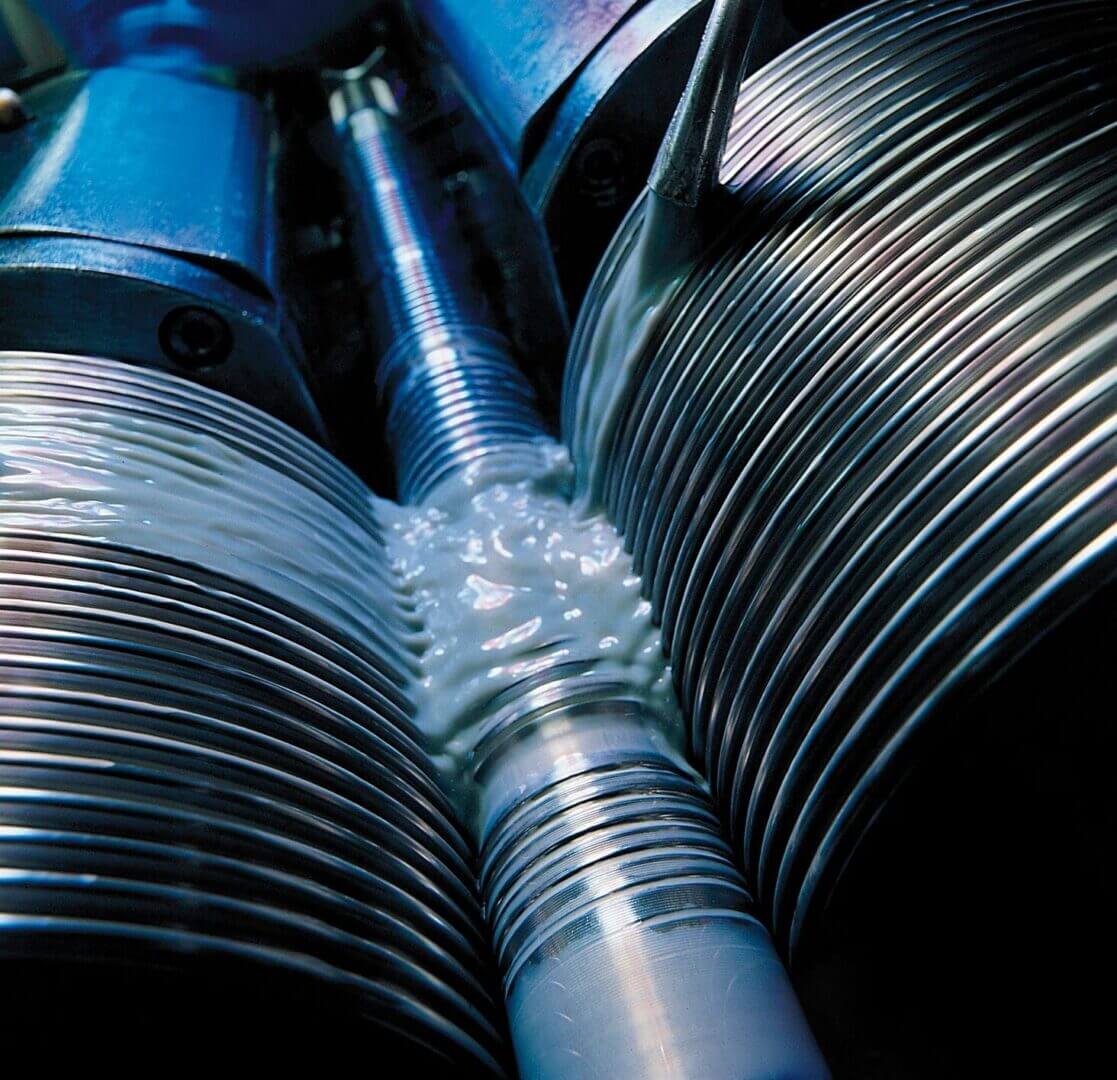
Service provider in development
The need to solve practical tasks is perpetual. Eichenberger Gewinde AG successfully exploits the opportunities this presents. The thread specialist has succeeded in establishing itself in the drive technology niche with its customized rolled lead screws. The Swiss company has clear goals: Rolling - the cold forming of threads and the production of lead screws (spindle and nut). Using state-of-the-art production methods and by developing new dimensions, Eichenberger supports the customer with "his" innovation.