Crude oil is the black gold of the earth - innovative and modern extraction technologies are required to obtain this precious resource. By the time the fossil fuel reaches our everyday lives in the form of the end products we are familiar with, it has not only had a history spanning millions of years, but has also come a long way. Eichenberger Gewinde AG has dedicated itself primarily to thread technology and has been rolling customer-specific, high-precision and sophisticated screw drives for almost seven decades. With a wealth of experience and technical know-how, it supports its partners on the way to their innovations. The thread specialist from Switzerland is aware that maximum adaptability of mechanical-dynamic functional elements contributes significantly to the success of projects in drive technology and takes advantage of these opportunities.
Deep drilling on the high seas
"Offshore" means "off the coast". In the field of oil and gas production, "offshore" refers to development in the sea. Hardly any other term better describes the clash between adverse climatic conditions and sensitive extraction technology. Wherever a hole is to be drilled, rock has to be crushed powerfully, precisely and efficiently. Today, highly intelligent drilling systems are used that move independently to or through the raw material deposits. It is not only the functionality of the drilling equipment that is remarkable, but also the extreme operating conditions. Deep down in the earth, temperatures are often the same as those we set in the oven at home to make pizza. In addition, there are static pressures of 500 to 1000 bar (car tires are only inflated to 2 bar), heavy blows and vibrations and the aggressive environment in the form of drilling fluids, sharp-edged cuttings, etc. Directional drilling technology allows drilling in different directions. With extremely complex systems, it is possible to change and determine the course of drilling in any direction. For example, where a deposit is located under a town or a nature reserve, a drilling rig cannot be erected. In this case, the drilling rig is erected a few kilometers further away and drilled vertically and horizontally towards the target.
Wanted: Robustness, high torque and slow rotation
In modern drilling technology, equipment is used that is unrivaled in space technology. "Normal" boreholes are usually several kilometers long. Despite the harshest conditions, the highly complex drilling equipment must function perfectly. It must not only drill quickly and effectively, but also be extremely reliable. Stuck drill groups cause enormous costs. In the steering system of these high-tech drill arms, the robust ball screw drive (KGT) type Carry guarantees the demanding steering work. High torque is required with slow rotation. The KGT from Burg (CH) manages the ambitious vertical and horizontal drilling sequences and is characterized by speed and precision. Pumping the oil or gas demands a lot from the mechanical components. Carry's high mechanical load capacity, the large achievable transmission ratios and the highly efficient, low-loss energy transmission really come into their own.
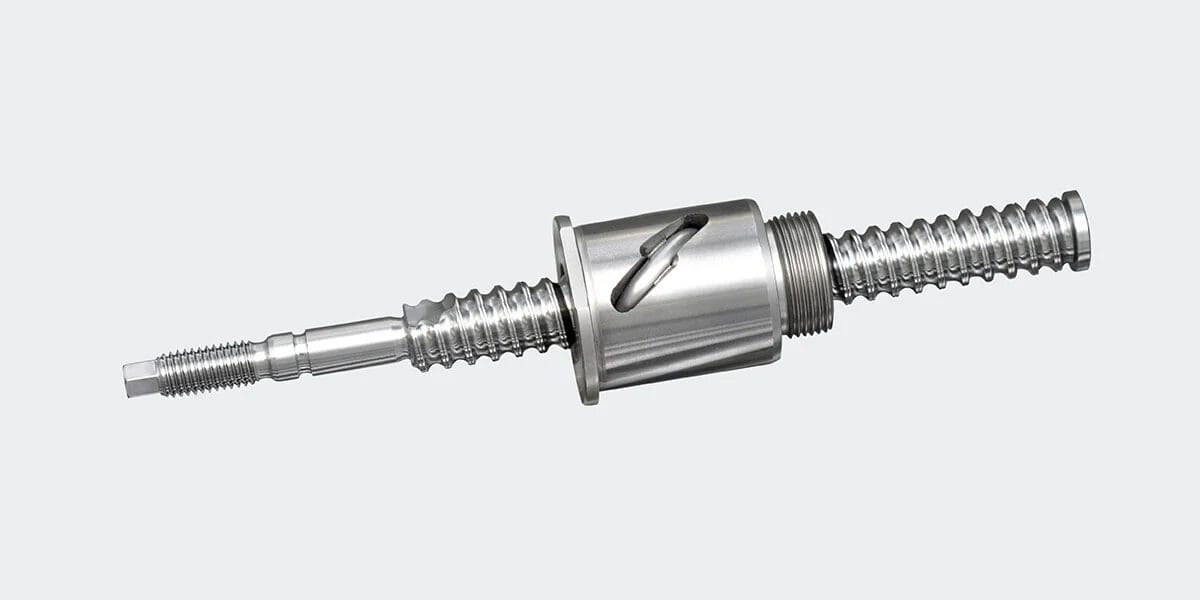
Found: Carry powerhouse
Based on the specifications, the extreme requirements for the static and dynamic load ratings, the speed, the torque, the dimensions and the geometric environment were known. The task was to determine the perfect ball screw drive and adapt the shape of the nut to the special specifications. Due to the high efficiency of over 0.9 and the associated energy efficiency, the KGT Carry provided the perfect answer. In the application in the steering of the drilling units, the tube ball return integrated in the Carry made of heat-resistant steel was particularly impressive. The ball return is bent and machined in a sophisticated process and is then integrated into the nut. The tube deflection underlines the robustness and load capacity of the Carry ball screw. With regard to lubrication at high temperatures and high pressure, the optimum solution was found in collaboration with a grease manufacturer. The special lubricating grease withstands. Heat, cold, corrosion, dirt, chemicals and salt water cannot harm it.
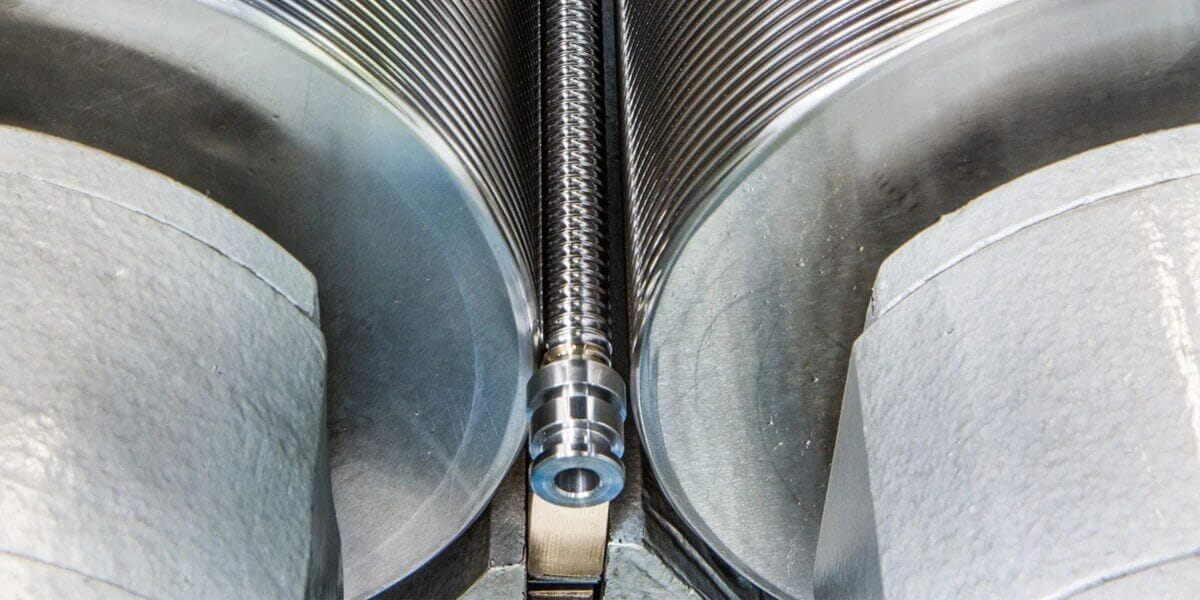
Ideal conditions due to cold forming
What makes the Carry ball screw drive so resilient and the ideal functional element for this application? Thread rolling produces very precise geometries with a high surface quality. The usual manufacturing processes for threads such as milling, turning or whirling are machining processes. These have the disadvantage that they interrupt the grain flow of the steel. On the other hand, thread rolling is a non-cutting process that does not cut the longitudinal fibers, but merely diverts them. Depending on the material, this results in an increase in strength of 30 to 50 %. At the same time, the surface in the profile hardens. This "smooth surface" offers little opportunity for dirt to accumulate. This is crucial for a long service life. Thread rolling also results in very good roughness values (~ Rz 1.0) on the thread flanks and in the base radius, resulting in significantly reduced notch sensitivity.
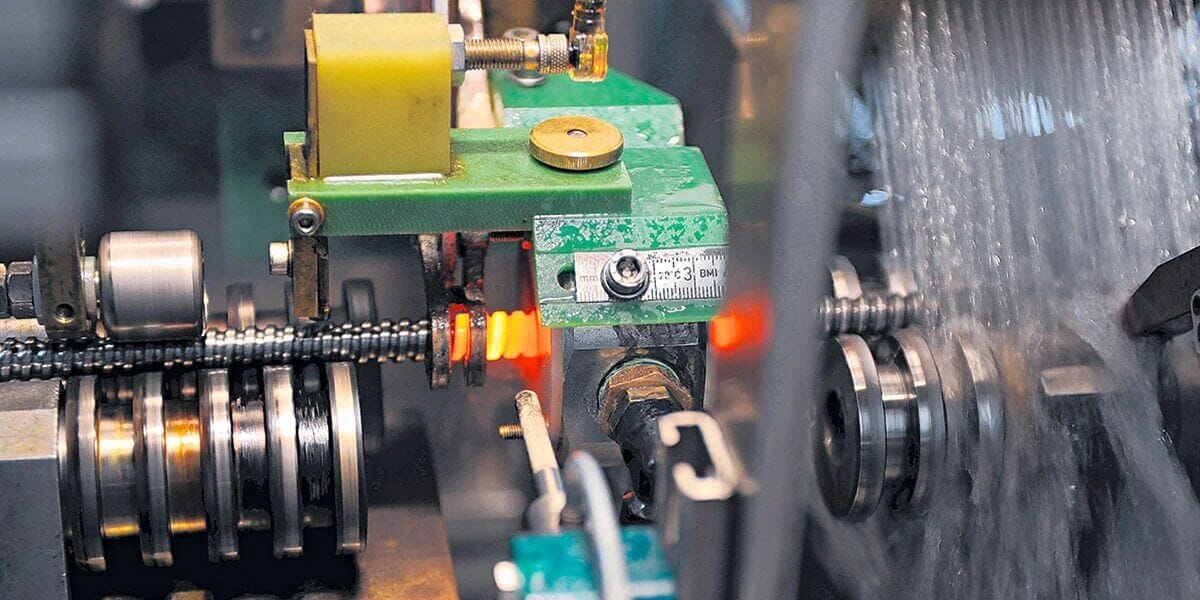
Always on the lookout for top performance
Thanks to its many years of experience in the field of in-house induction hardening, the Eichenberger thread roller has also acquired a great deal of expertise. While a hardening store is dedicated exclusively to hardening steel, it strives to achieve the best possible combination of hardness and precision. What sounds so simple is only possible if the team works very closely together. Proximity to the customer and a feel for their needs are basic requirements. Thanks to advanced machinery, state-of-the-art production methods and the fact that development, production and quality assurance come from a single source at Eichenberger, prototypes can be produced within a very short time. The step to series production is then already in advance. So when the inventor of the product is also its most economical manufacturer, something really can be achieved!
Service provider in development
The need to solve practical tasks is perpetual. Eichenberger Gewinde AG successfully exploits the opportunities this presents. The thread specialist has succeeded in establishing itself in the drive technology niche with its customized rolled lead screws. The Swiss company has clear goals: Rolling - the cold forming of threads and the production of lead screws (spindle and nut). Using state-of-the-art production methods and by developing new dimensions, Eichenberger supports the customer with "his" innovation.