We have set ourselves the goal of continuously developing our core competence "cold forming the lateral surface of round parts". The world of drive technology is constantly changing, growing and facing new challenges every day. Proximity to the customer and goal-oriented dialog with our partners are the basic prerequisites for sophisticated individual solutions.
Forward with healthy innovation
Speed, weight, precision and maximum service life meet compact, adaptable, robust, safe and economical products. These quality features in turn interact with resource and energy efficiency. Today, the ideal mechanical component must meet the highest performance requirements and should tend to cost less and less. The intensive and successful cooperation between Eichenberger and the technology leader Festo, Esslingen / Germany, has existed for many years. With the takeover of Eichenberger Gewinde AG by Festo AG in 2016, valuable synergies can be realized. This cooperation and the combined innovative strength will make a difference in the fields of electromechanical drive technology in the future.
Servo press technology in the age of Industry 4.0
Electric servo presses, also known as joining modules, are used for force-displacement-monitored joining by press-fitting, for joining by forming such as riveting or clinching, for embossing, punching or, for example, for testing springs. The specifications include high precision, short cycle times, immense pressing forces and often also high speeds. A typical area of application for servo presses is automated assembly processes that require high repeat accuracy and monitored joining quality with the option of documentation. Universally applicable joining modules are used in the automotive industry, aerospace technology, medical technology, mechanical engineering, electrical engineering and many other sectors.
The increasing fusion of modern information and communication technology with classic industrial processes is changing the various production areas in the sense of Industry 4.0. This also affects forming technology. The massive increase in the quantity of data, the complexity in the networking of systems and the required changeability and flexibility of components demand a general understanding of digital, fully automated production processes. In-depth knowledge of the structure and programming of digital plant networks (control systems, peripherals, drives, safety technology) is essential. In modern servo presses, such as the YJKP servo press kit from Festo, a lot of data is already collected and evaluated, be it on the stroke, ram position, feed speeds, braking and acceleration ramps, etc. The YJKP servo press kit therefore already provides Industry 4.0 features.
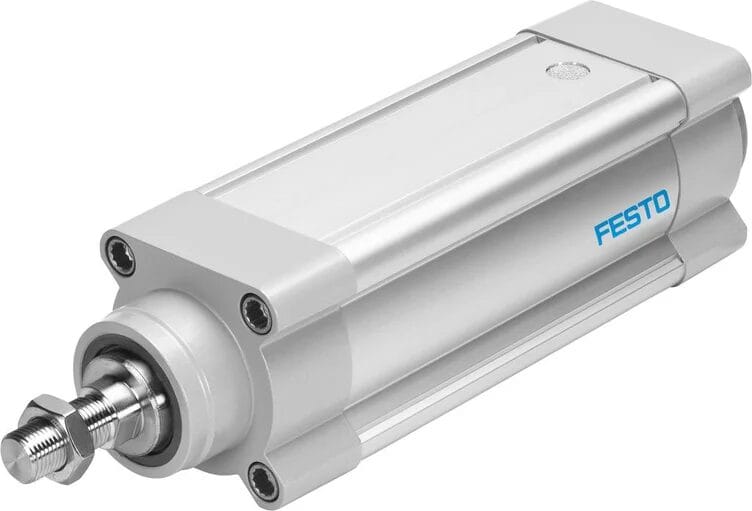
17 kilonewtons of maximum force and a stroke of 1500 mm (Photo: Festo AG & Co. KG)
Carefree package servo press kit YJKP
Presses are often oversized. By their own admission, users utilize just 10 % of the output of a preconfigured press. The YJKP servo press kit from Festo addresses precisely this issue. It enables electric press applications with up to 17 kN. Integration into your own system concept is simple and the price is unbeatable. The modular servo press kit provides exactly the software functions that users really need for their application. This gives them an optimum cost-benefit ratio for their high-precision and repeatable press system. This flexible, pre-assembled system solution consists of modular operating software and coordinated standard components from Festo - the ESBF electric spindle drive, the EMMS-AS motor, the CMMP-AS motor controller, the CECC-X controller and a force sensor.
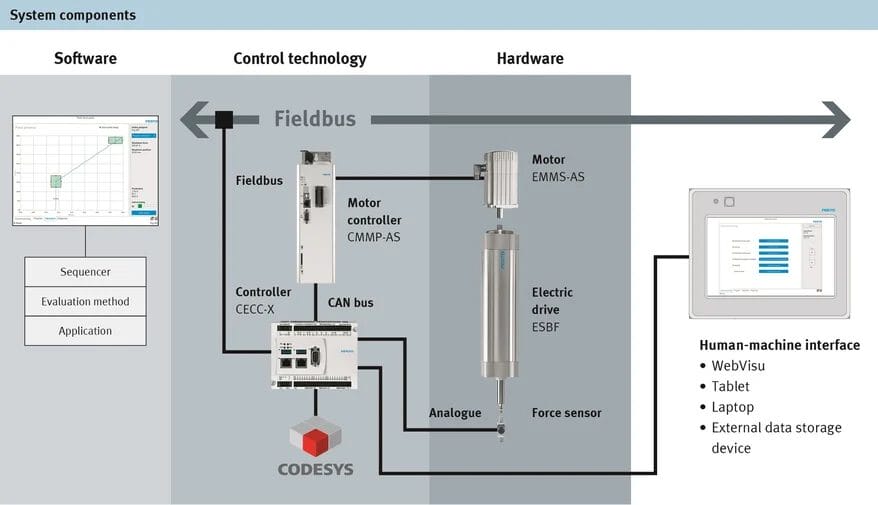
The system components of the servo press kit (Photo Festo SE & Co. KG)
The ball screw drive centerpiece ensures peace of mind
In the modular system, users can choose, for example, a force range from 0.8 to 17 kN, a stroke length from 100 to 400 mm or an axial or parallel motor attachment. The acceleration is an incredible 25 m/s². The high-precision electric cylinder ESBF is at the center of the matched components. We are talking about a powerhouse that shines throughout its entire service life of more than 10,000 km without relubrication during the perfect pressing process. It contains the real heart of the system, the cold-rolled drive element! The electrically driven ball screw drive from Eichenberger converts the rotary movement of the motor into a linear movement of the piston rod. The impressive efficiency of over 90 % ensures optimum drive performance. The induction-hardened ball screw of the Carry series impresses with its extremely high load capacity, flexibility and spindle diameters from 4 to 40 mm, not to mention its attractive price. If the fastest movements are required, lead screws with large pitches are needed. Carry combines speed, precision and minimum space requirements. Spindle pitches from 5 to 40 mm are used in the servo press, depending on size and customer requirements.
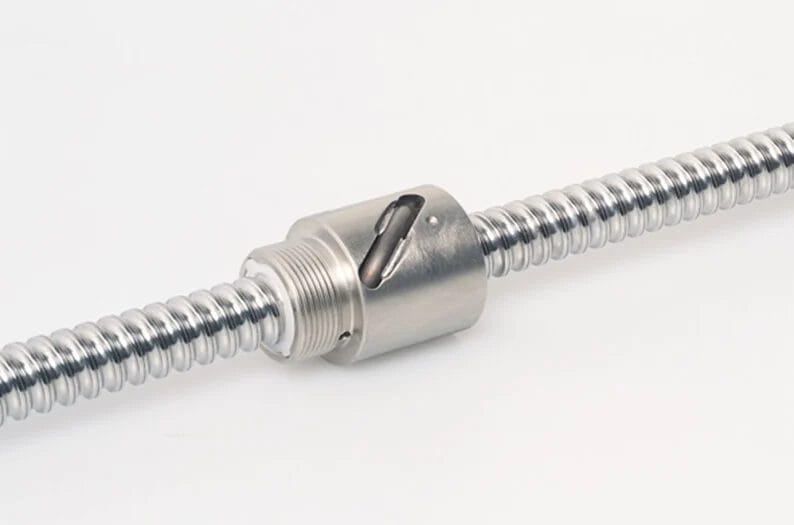
What makes the Carry ball screw drive the ideal functional element?
The core competencies of Eichenberger Gewinde AG lie in thread rolling and hardening. A thread is produced by deforming a workpiece very dynamically under enormous force between two rotating rolling tools. Thread rolling leads to a considerable increase in strength (depending on the material, 30 % to 50 % are possible), good roughness values and reduced notch sensitivity.
The usual manufacturing processes for threads, such as milling, turning or whirling, are machining processes. These have the disadvantage that they interrupt the grain of the steel. On the other hand, thread rolling is a non-cutting process that does not cut the longitudinal fibers, but merely diverts them. The result is a "smoothly rolled", compressed surface, which is essential for a long service life of the spindle. A huge advantage of the rolled KGT spindles is that the profile with the ball raceway on the thread roller is transferred 1:1 to the spindle. This means that the ball raceway of the spindle is 100 % identical to the outside diameter. The end machining of the spindle turned over the outside diameter (collet chuck etc.) leads to optimum coaxial values. The rolling friction coefficient of steel balls is 0.003 to 0.001 compared to the sliding friction of steel on steel (lubricated) 0.1 to 0.05. These excellent sliding properties ensure minimal abrasion and offer little surface area for contamination. This makes low-noise rolling of the balls child's play.
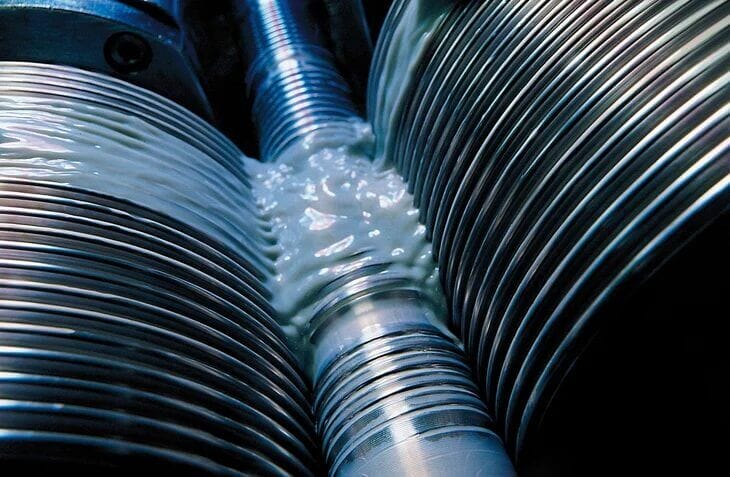
While a pure hardening store is dedicated exclusively to hardening steel, we strive to achieve the best possible combination of hardness and precision. The variety of dimensions poses a challenge that should not be underestimated. It is particularly important to determine the ideal hardness tolerance in order to achieve optimum precision. The smaller the dimensions, the more specialist knowledge and intuition are required for hardening.
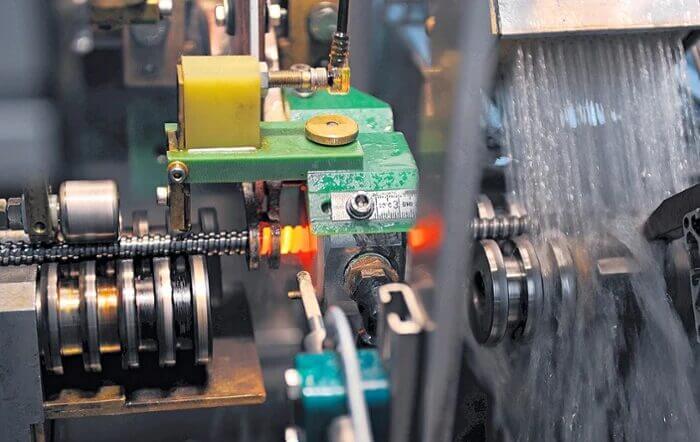
When used in the ESBF electric cylinder for the YJKP servo press kit, the Carry ball screw also impresses with its integrated tube ball return, which has been tried and tested thousands of times. It underlines the robustness and load capacity of the Carry ball screw.