Mechanical engineering is a key industry in the German economy. Fife-Tidland GmbH in DE-Kelkheim, for example, developed the first web guiding system over 75 years ago (e.g. precise positioning when winding and unwinding a wide variety of web-shaped materials). The demands placed on next-generation machines are constantly increasing in the same way as the demands placed on mechanical drive elements. The mechanical engineering industry often requires drives that not only fulfill a specific function. In addition to functionality, quality and adaptability, the focus is also on delivery times and competitiveness. This fact has allowed the dedicated inventor of the web guiding and monitoring system and the Swiss-based company Eichenberger Gewinde AG to grow together. The companies have been working together on projects for 15 years now and are mastering new challenges together.
Amazing adaptability for edges, lines and images
You realize how difficult it is to roll things up properly when you drop a roll of kitchen paper or aluminium foil. This is the crux of the matter with controlled web guiding systems. What technical solutions can eliminate the problems of the web "running" and achieve the desired winding result?
Fife-Tidland GmbH provides the answer: Sensitively accurate web guiding systems and width measurement provide the efficiency required to improve the processing steps at every stage of the material web processes. Downtimes are avoided and consistent quality is guaranteed.
When striving to achieve dynamic equilibrium, a belt generally tends to align itself at right angles to a guide roller. Various factors such as strength, stress distribution and mass inertia come into play here. These factors need to be controlled. From the thinnest plastic film to the thickest steel strip, from very narrow webs to the widest rolls, Fife-Tidland GmbH supplies the full range of advanced web guiding systems and products for every application. In addition, the operator is supported by an easy-to-use web monitoring system.
How it works
The processors form the heart of the electronic control system. In combination with high-precision, versatile sensors (edge control, line or print image control or center control) and backlash-free drives, these processor units ensure an extremely precise control system with high dynamics on the running web. A wide variety of rotating frame systems offer the possibility of precise corrections by guiding the web at an offset angle as it passes through the control section. The rotary movement of the frame shifts the material web to the required position in the process. The work steps during set-up, emergency shutdowns or when converting to other widths are easy to manage and the systems can be used in the smallest of spaces.
Customer satisfaction through optimal communication
Eichenberger Gewinde AG has set itself the goal of supporting its partners in the successful realization of their innovative ideas. The adaptability of mechanical-dynamic functional elements, energy efficiency and cost-effectiveness are decisive for the future of drive technology projects today, and the thread roller is aware of this. Close contact and needs-oriented dialog with the customer play a major role in this.
The developer and manufacturer of web guiding systems recognized the advantages of the cold-rolled ball screw drive (KGT) from CH-Burg a long time ago. He relies completely on Eichenberger's flexibility and know-how and is a returning customer. Fife and Tidland products are sold worldwide through Maxcess International, Inc. Around 10 different and perfectly adapted ball screw types are used in the various systems. These are customer-specific special ball screws or the FGR and ZYI series in dimensions from Ø 8 mm, pitch 1 mm (8 x 1) to Ø 32 mm, pitch 5 mm (32 x 5). The cold-rolled KGTs ensure accurate movement in sometimes extremely confined spaces.
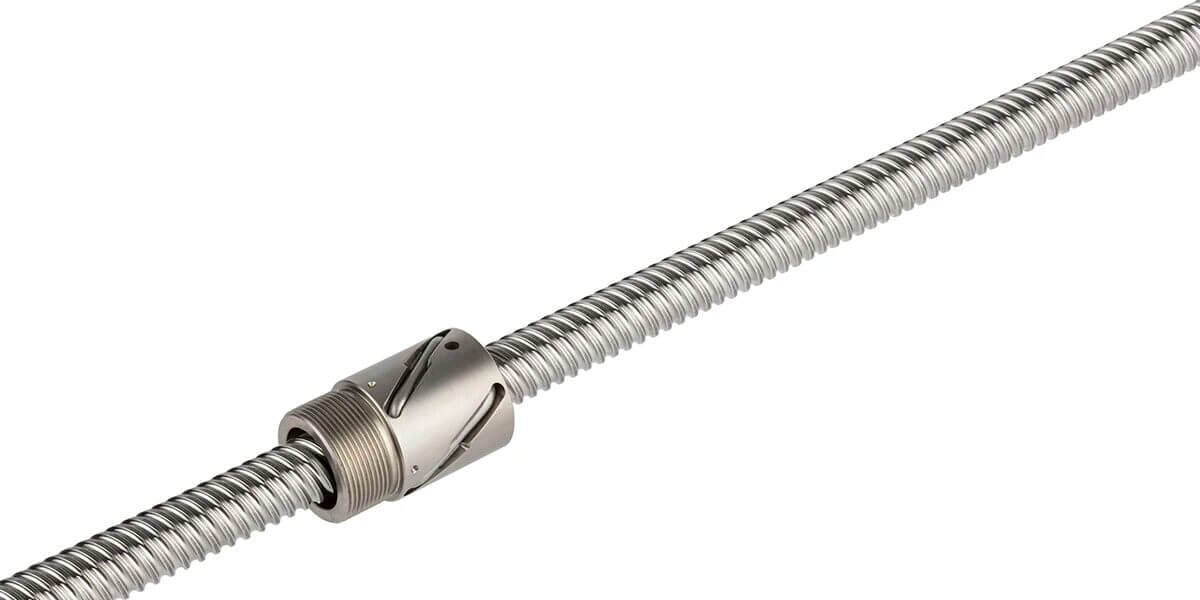
Small function with a big effect
A spindle is controlled directly via a motor, a gearbox and belt drives. This allows rotary movements to be converted into linear movements. In the case of web guiding systems, the ball screw drive sets the corrective movement of the sensor-controlled actuator in motion. Accordingly, thrust, speed, stroke and precision are integrated in a single product and the optimization of the material web position can be perfectly controlled (with the aid of rotating frame or other systems). The advantages of KGTs include their high efficiency of over η 0.9 and the resulting energy savings. Due to the power transmission with balls, the required drive power can be reduced by around two thirds.
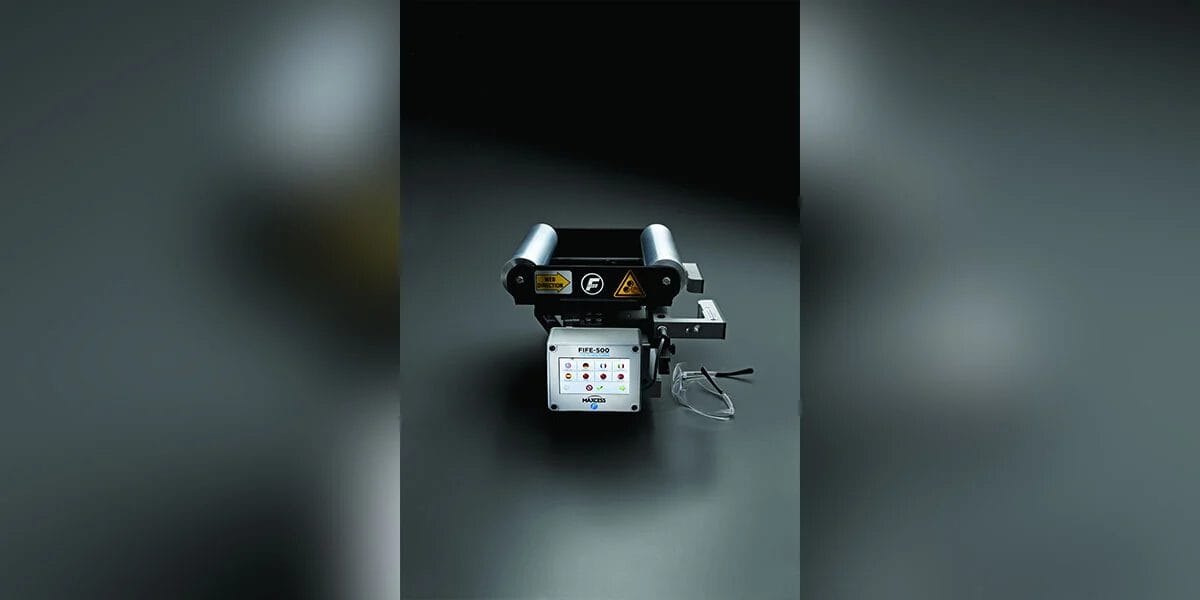
target position, the sensors generate a signal. The signal processor records this signal FIFE-500
web guiding system and controls the drive unit, which realigns the rotating frame until the web position is corrected. The rotary movement takes place around an axis that is perpendicular to the
mounting frame is located on the outer edge of the infeed roller.
Flexibility is no accident
The partnership-based cooperation has led to Eichenberger today equipping the entire Fife-Tidland / Maxcess product range with special ball screws from diameter 8 to 32 mm. This above-average flexibility is the result of specialist knowledge accumulated over more than six decades and the fact that development, production and quality assurance come from a single source. This in turn also speeds up the production of prototypes, which can be delivered within a very short time. Even rolling tools can be manufactured "in house". Thanks to these factors and an advanced machine park, flexible and competitive production is possible even at expensive locations. The thread specialist is able to deliver customized solutions that provide optimum functionality and maximum energy efficiency and are also cost-effective.
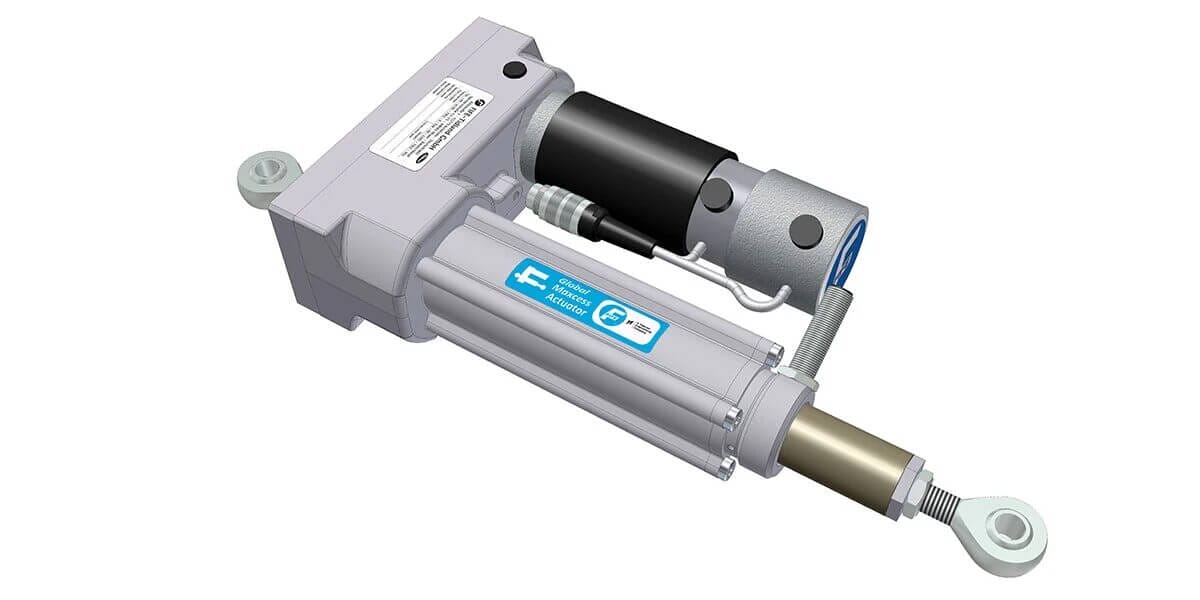
Technical achievements - the recipe for the ideal ball screw drive
Cold forming
A thread is created by deforming a workpiece under enormous force between two rotating rolling tools. As the rolling tool profiles penetrate the surface of the workpiece, the cold material is pressed into the base of the thread rolling tools and rolled up to the nominal dimension. The usual manufacturing processes for threads are machining. In other words, milling, turning or whirling. However, they all have the disadvantage of interrupting the grain flow, which determines the force flow under the load of use. Thread rolling, on the other hand, is a non-cutting process that does not cut the longitudinal fibers, but merely diverts them. At the same time, the surface hardens, which is crucial for a long service life. Furthermore, this cold forming process produces very good roughness values (around Rz 1.0) on the thread flanks and in the base radius, resulting in significantly reduced notch sensitivity. Cold rolled and ground threaded spindles differ in many respects. The price plays a decisive role.
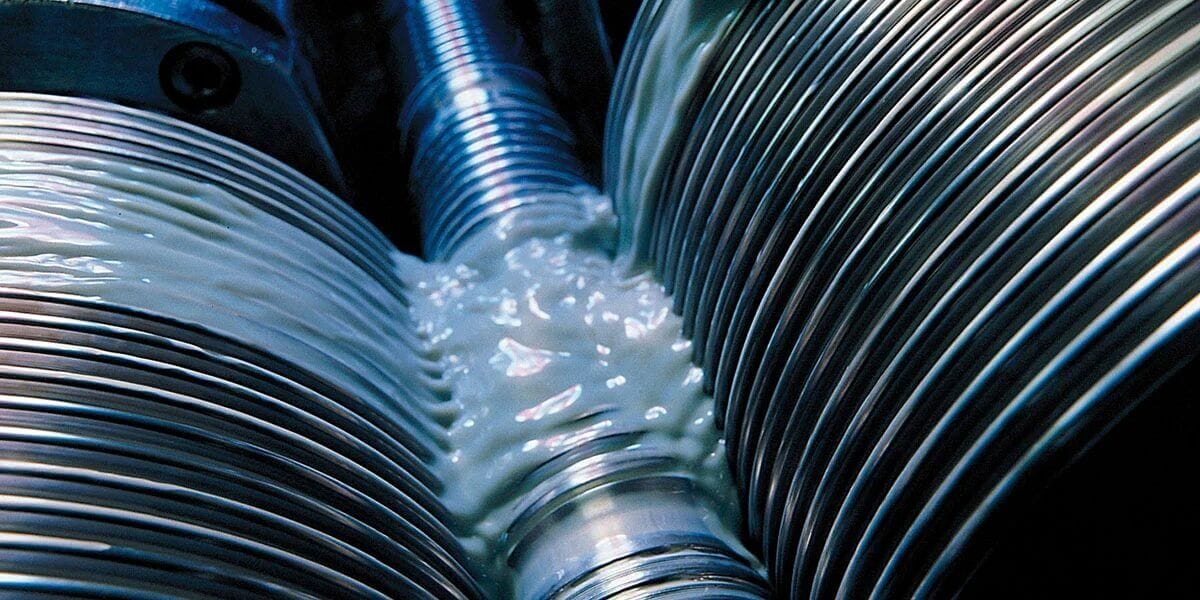
Hardening
While a pure hardening store is dedicated exclusively to hardening steel, the thread specialist strives to achieve the best possible combination of hardness and precision. The variety of dimensions poses a challenge that should not be underestimated. It is particularly important to determine the ideal hardness tolerance in order to achieve optimum precision. The smaller the dimensions, the more specialist knowledge and intuition are required for hardening. Eichenberger specializes in hardening small diameters. As this process is a sub-step in the overall production process, induction hardening can be perfectly coordinated in-house. Here is one example: The 6 x 1 mm ball screw must have a hardness of 700 - 800 HV in the ball contact area. It is necessary that the core diameter of 5.0 mm (thread root) is also hard. In addition, it must be ensured that the core of the screw remains soft, as this is the only way to guarantee the necessary elasticity and load-bearing capacity of the screw.

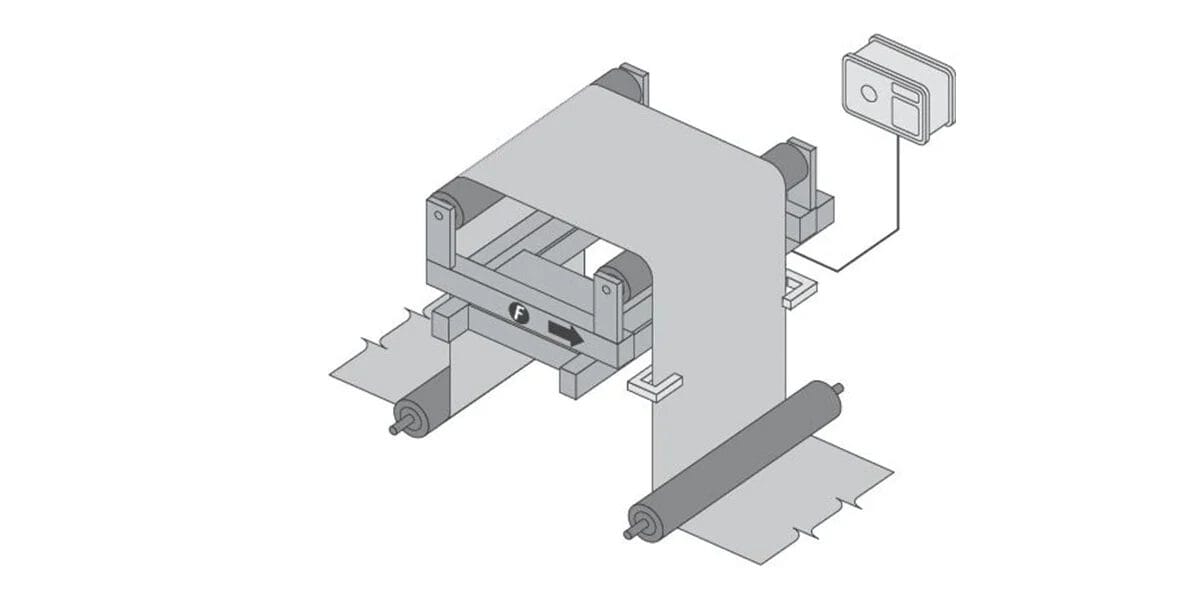
Service provider in development
Thread forms that are outside the norm, new dimensions or exotic materials are the challenges Eichenberger is looking for. A ball screw drive is actually a simple motion element, but if it has outstanding characteristics such as dimensional diversity, high load capacity, efficient efficiency, excellent precision values and service life, it opens up an extremely wide range of applications. The fields of application for Eichenberger's cold-rolled KGTs range from medical, electrical and automotive engineering, through the textile and household appliance industries, to automation and general mechanical engineering.