When the sky is dark at dusk and the ISS is illuminated by the sun, you can see it from Earth. The International Space Station shines like a bright star. It is bigger than a football pitch. At an altitude of 400 kilometers, it flies at such a speed that it defies the Earth's gravitational pull. Swiss thread specialist Eichenberger once again confirms that it combines customer wishes and performance requirements with solutions, as three ball screw drives master docking with the ISS in orbit.
No matter how specific the requirements are
Design engineers are regularly faced with the task of determining the appropriate drive technology for the realization of linear movements. High infeed accuracies and oscillating movements of high frequency with the smallest strokes or high dynamics in continuous operation often have to be mastered. The focus is on safety and reliability. Small installation space with high loads is often a challenge. Maintenance and service life and, last but not least, costs also play an important role. The demands on mechanical drive elements and the requirements in the respective fields of application are increasing in equal measure. Ball screw drives (BSS) are among the most frequently used drive systems in many industries. The advantages of these drive systems lie in their high efficiency and energy efficiency.
Eichenberger's spindle technology, thread rolling (cold forming of the lateral surface of round parts), combines maximum load capacity and force density with enormous dynamics and precision at maximum running performance.
"The most important thing in a conversation is to hear what has not been said." - Peter F. Drucker
At Eichenberger, the focus is always on the customer: actively listening and asking questions, advising, designing, building, testing, optimizing and producing. Only through the targeted exchange of information and ideas can needs be fully understood and implemented. In this way, the thread specialist, relying on its own strengths, adapts its products and its value chain to the constantly increasing international change. The thread specialist lives "Acting with foresight instead of reacting" as a vital part of its corporate culture. Its customized ball screws are used everywhere, from medical, electrical and automotive engineering to automation and even aerospace.
"The path to core competence is the same in every field: persistently cracking special nuts." - Karl Heinz Karius
Over almost seven decades, the wide range of customer tasks have made the thread roller from Burg (CH) an experienced and sought-after specialist. Extremely efficient, fast production is the rule at Eichenberger. Prototypes, including thread rolling tools if necessary, can be produced within a short time. This is only possible because development, production, quality management and sales are perfectly integrated in-house. Thanks to this factor, production can be flexible and competitive. Today, the most unusual customer solutions are developed on request. The impossible is realized in an extremely economical cold rolling process.
Space rendezvous - Eichenberger's screw drives make it possible
Success stories are the goal of our work. It is not uncommon for solutions for the most exotic special applications to begin with inspiring conversations. A project was launched in Burg in 2015 with the world's leading supplier of products for the space industry. The aim of this collaboration is to carry out dockings during a space rendezvous between the ISS and the innovative, reusable space glider from 2020. The "300 % safe" and functional docking unit is central to this. At the heart of this docking system are three strong, corrosion-resistant ball screw drives with end cap ball return, Carry type KGE, 16 x 16. Reliability is the top priority for the space shuttle service. Robustness and resilience in the harsh, inhospitable orbital environment play a key role. In the same way, meticulous accuracy is crucial.
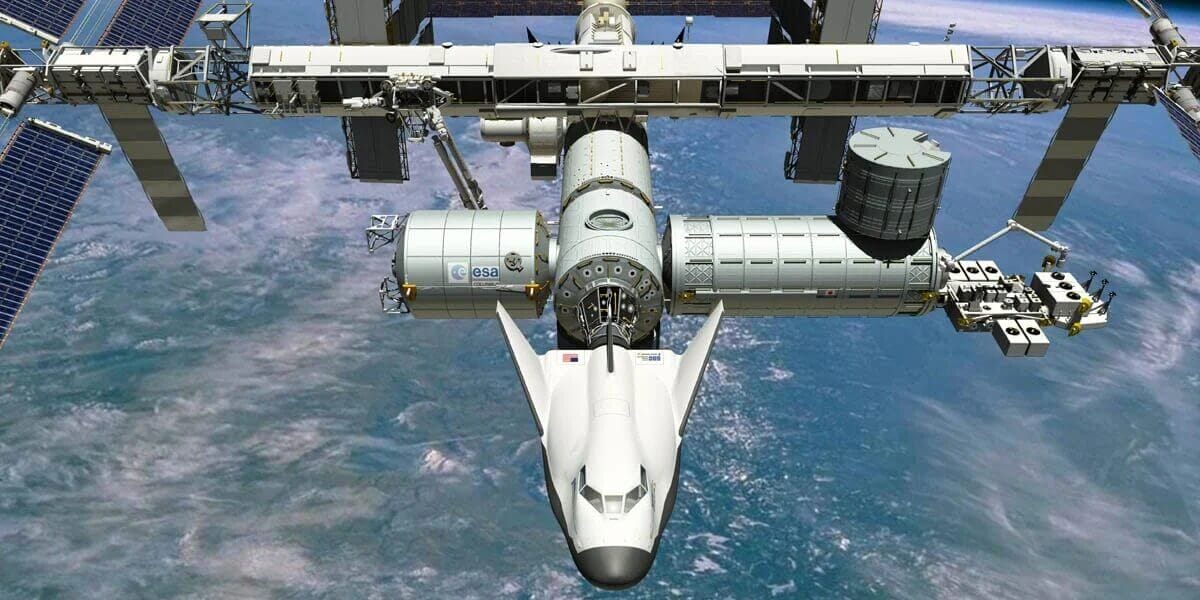
The new spacecraft is launched into low-Earth orbit atop the Atlas V launch vehicle. It flies with or without a crew and can land at any normal airport. The space glider can carry up to seven astronauts. The space glider could, for example, serve as a research platform, transport people or freight into space or be used to actively remove space debris from orbit. With the docking unit, in which Eichenberger's Carry ball screw drives guarantee a precise, secure docking process, it is possible for the dream chaser to dock with the ISS, the inhabited station in orbit. At 28,800 kilometers per hour in zero gravity, the flying laboratory only needs 92 minutes to orbit the Earth once. Astronauts living and working on the station therefore experience 16 sunrises and sunsets every day.
The challenge of space travel - extreme conditions
The first major hurdle after the grueling rocket launch with extreme acceleration and vibration is the vacuum. It affects everything that is liquid or can vaporize. This also includes lubricants. Greases, which are solid on earth, evaporate in a vacuum, which is why moving parts have to manage without lubrication despite the highest service life requirements. Temperature extremes pose a further challenge. The temperature of the components in an Earth orbit depends on the material that is irradiated. For the docking station, temperatures of - 50°C to + 90°C are assumed. In addition, ultraviolet light, X-rays, particles with a high energy charge and atmospheric atoms stress the material, making it more susceptible to corrosion. Eichenberger proves that the exceptional performance features of the Inox ball screw Carry with the integrated high-performance plastic in the ball return can withstand the aggressive environment in space in a functionally reliable, corrosion-free and wear-free manner.
Competence put under the microscope
What makes the Carry ball screw drive so resilient and the ideal functional element for this application?
Thread rolling using the cold rolling process produces very precise geometries with a high surface quality. In contrast to grinding, milling or turning, thread rolling does not cut the longitudinal fibers of the material, but deflects them. The result is a compressed, smoothly rolled, extremely resilient surface, which is essential for a long service life of the spindle. The roughness values of around Rz 1.0 on the thread flanks provide a major advantage. The rolling friction coefficient for steel balls is approx. 0.0013 compared to sliding friction steel on steel (lubricated) 0.1 to 0.05. The excellent sliding properties of the cold-rolled ball screw ensure minimal abrasion and offer little surface area for contamination. This makes low-noise rolling of the balls child's play.
Convincing technology HARD-INOX®-P treatment. Meeting the highest requirements in terms of surface hardness and corrosion resistance of stainless steel has been achieved with the innovative Hard-Inox®-P treatment. In this process, the performance of the edge structure of corrosion-resistant steel is significantly increased by high-temperature nitriding (the surface hardness reaches 550 to 750 HV with a hardening depth of 0.1 to 1.0 mm). The great benefit lies in the increase in service life and value retention. The trick is to master distortion and dimensional changes despite high-temperature treatment. The aim is to achieve the perfect combination of hardness and precision.
The ideal partner from one-off production to series production
The wheel of mechanics cannot be reinvented. And yet it is Eichenberger's ambition to keep pushing the boundaries of the cold-rolled KGT. Competence goes beyond knowledge, or to put it another way, competence is problem-solving knowledge. Every newly developed spindle drive is included in the thread roller range. Over the decades, this has resulted in a huge selection of ball and lead screw drives.
The developers always try to start with a standard nut and spindle and adapt these components to the application-specific requirements. This results in a decisive price advantage. The challenge for designers in Switzerland, a high-price country, is to develop very high technical value in a competitive product that meets market requirements. Technological knowledge, research and development are just as necessary as the willingness to change and the mastery of efficient manufacturing processes.
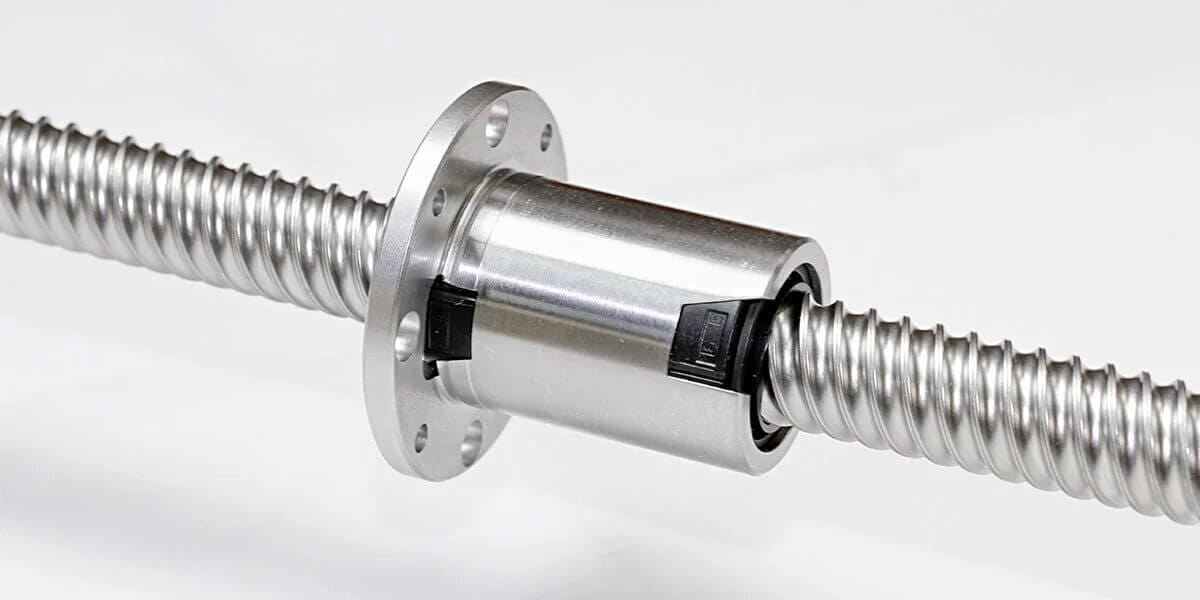
The need to solve practical tasks is perpetual. Eichenberger Gewinde AG is successfully exploiting the opportunities this presents and has succeeded in establishing itself in the drive technology niche with its customized rolled screw drives. The Swiss thread specialist has clear goals: The rolling (cold forming) of threads and the production of lead screws (spindle and nut). Using state-of-the-art production methods and developing new dimensions, Eichenberger supports its customers in "their" innovation.