Flexibility and adaptability, along with reliability and safety, are not only the key principles of the thread specialist Eichenberger, but are also the most important requirements for the new generation of threaded fasteners.
- Gearshift systems for trucks or
- for automatic vehicle door systems
Energy efficiency, resource conservation, noise and pollutant reduction play a key role in sustainable mobility concepts. The aim of technical progress is not just to achieve more, but to be able to do many things better with new technologies and processes. Supporting customers on the way to innovative individual solutions, with sound know-how and using state-of-the-art production methods - these are the goals that Gewinderoller, based in Switzerland, pursues every day.
Ball screw drive in use with system-optimized clutches
In one of the first automated gearshift systems on the market, Eichenberger succeeded in developing the key design element for the latest and pioneering automatic version of the clutch and bringing it from individual production to series production. With the cold-formed steel ball screw spindle, diameter 12 mm, pitch 3 mm, the new clutch can be fully engaged at low engine speeds simply by operating a switch. In addition, the clutch actuation is adapted to the information from the tilt sensor and to the required starting gear. In this way, the engine speed is increased if necessary for a clean start. The clutch does not slip during gear changes, i.e. the speed of the mechanisms in frictional contact with each other does not deviate. It therefore only serves to separate the transmission from the engine. These functions effectively protect the clutch and other drivetrain components from mechanical overload.
Frequent gear changes are often unavoidable in trucks. The more frequent the gear changes, the faster the clutch disk wears out and the more likely it is that the clutch will require premature maintenance. Of course, wear is not only related to the frequency of this shifting action, but also to the type of shifting. The closer you get to an optimally timed and perfectly executed operation, the more likely it is that wear will be reduced. This new type of electric clutch system therefore leads to less wear, which has a direct effect on operating costs as well as increasing service life. Noticeable fuel savings are also achieved.
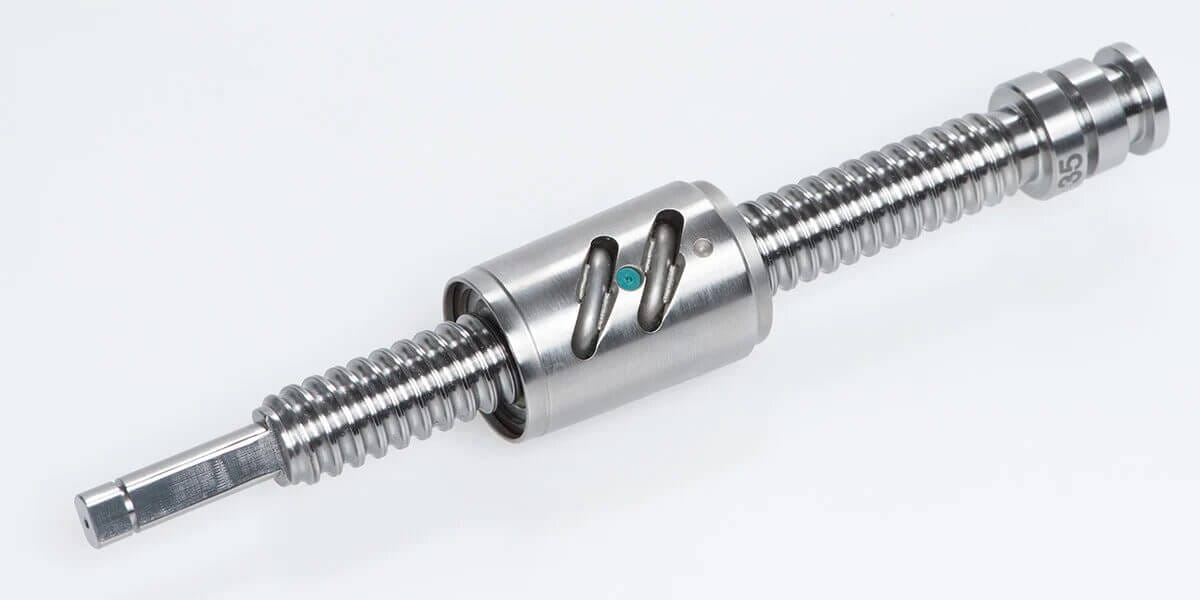
There's no such thing as impossible
This cleanly coordinated clutch process demands the utmost in terms of dynamics. A load of 3500 N is required in 0.02 seconds. What sounds so simple required a whole 6 years of basic research and development time in the areas of dynamics and lubrication. Only a ball screw drive (KGT) can withstand these concise requirements between dynamic forces and movement variables. The robust precision KGT Carry from Eichenberger masters these hurdles with ease. Thread rolling has an extremely positive effect on the roughness values of the thread flanks and the base radius, resulting in very low notch sensitivity.
Lifetime lubrication is demanding and tricky to guarantee. We are talking about 7-digit load changes at around 4000 revolutions. It was not only the impressive efficiency of the Carry ball screw drive of over 90 % over the entire service life that required extensive testing; in some cases, the endurance runs extended over 9 months and lubrication tests to achieve the service life took more than 2 years. For the KGT 12 x 3, Eichenberger used the tried and tested steel deflection tube system. As a result of the developments, a highly efficient connection of the deflection tube could be realized.
Sliding door systems for high-speed trains
Delays and unforeseen incidents can easily occur with automatic boarding systems. The design of sliding door systems therefore has a decisive influence on passenger safety and comfort, as well as on economic efficiency. High-speed trains, for example, reach speeds of over 300 km/h. Imagine the forces at work, also in terms of air resistance and wear. Resistance, for example, increases as the square of the speed. So if the speed doubles, the air resistance quadruples. Great effort, robustness, precision and reliability must be guaranteed in the tightest of spaces. The doors must move easily and quickly. In the event of a power failure, the spindle-nut system must not be self-locking. Emergency opening must be possible by hand at any time.
Heart of door operator - Steep thread spindle aluminum
In current materials research, "cheaper, lighter and stronger" are often the key trends. Weight savings, CO2 emissions and fuel consumption can be reduced with light metal, and greater ranges can be achieved. Aluminum offers light weight with consistent stability, high load-bearing capacity and excellent machinability, which fascinates Eichenberger's developers enormously.
At the heart of these door systems is the linear drive. The aim of the designers from CH-Burg was to develop a more cost-effective solution for the movement tasks inside these drive units. It is therefore a further development of the spindles that are already used in sliding door applications.
Groundbreaking innovations are always the result of hard development work. Eichenberger has succeeded in producing the cold-rolled aluminum lead screw with a special 20 mm diameter profile and 80 mm pitch. The innovative combination of the special hard-anodized aluminium lead screw 20 / 80 and the plastic nut (nut material depending on the application) is designed in such a way that it is possible to manufacture the lead screw using the cold forming production process. The thread rolling process is known to have remarkable advantages in terms of hardening, roughness values and notch sensitivity. The special profile of the thread provides a completely different support. The tilting moment is absorbed via the outer diameter of the spindle, which ensures smooth operation and prevents jamming.
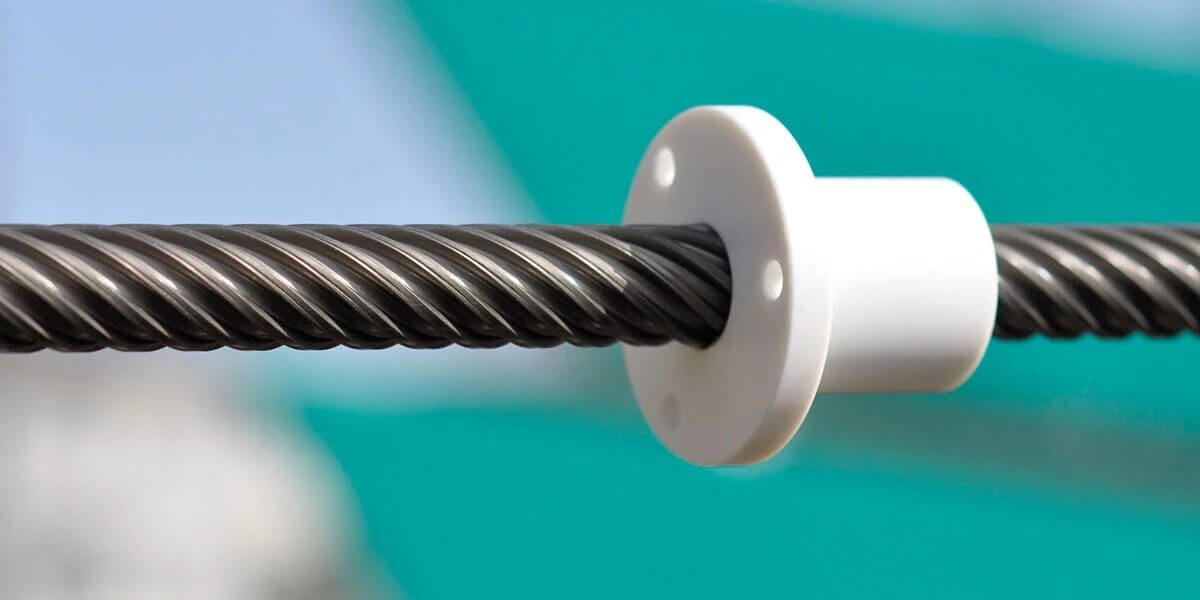
Only when the various components (ideal raw material/alloy, flawless cold forming, thread rolling tools specially manufactured by Eichenberger for the rolling process) are in perfect harmony can the material flow be optimized for a high pitch ratio of 80 mm. The Swiss thread specialist is able to offer development, production and quality assurance at the same time, so the flexibility in the manufacturing process or in the creation of prototypes, including thread rolling tools, is remarkably high. Potent know-how is also essential when it comes to designing the tools for the internal thread of the plastic nut. Thanks to these factors, production can be flexible and competitive even at expensive locations.
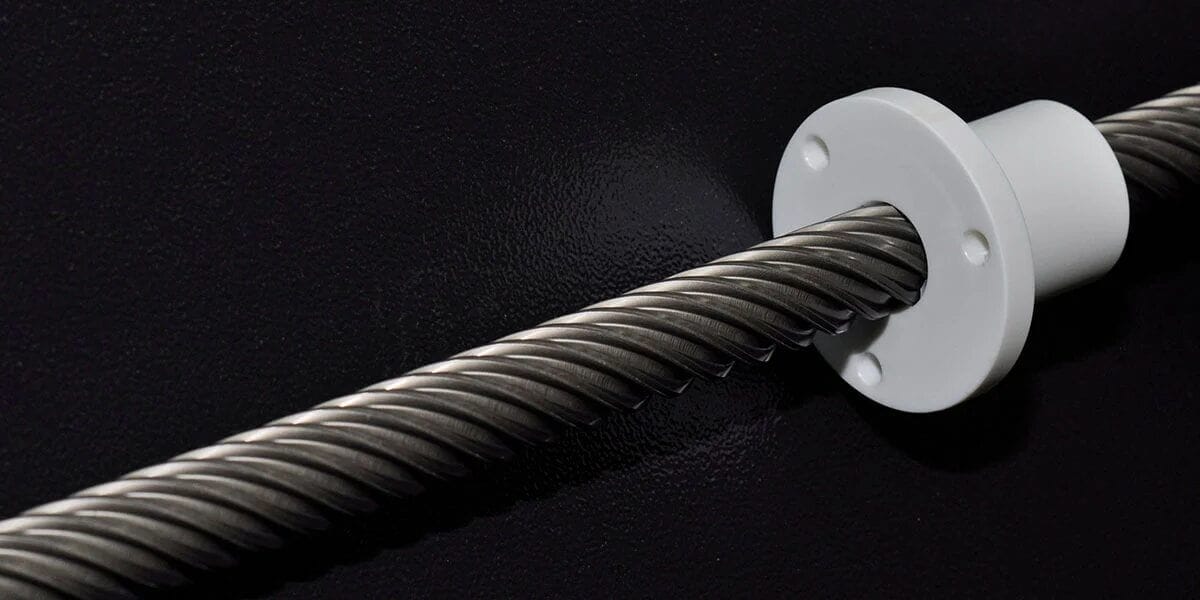
What is thread rolling?
The core manufacturing competence of Eichenberger Gewinde AG lies in thread rolling. The thread profiles of Eichenberger thread spindles are therefore manufactured exclusively using this process. Thread rolling (often also called thread rolling) is the cold forming of the outer surface of round steel parts. A thread is produced by deforming a workpiece under radial-dynamic force between the two rotating rolling tools. As the rolling tool profiles penetrate the surface of the workpiece, the cold material is pressed into the base of the thread rolling tools and thus rolled up to the nominal dimension.